In the realm of modern manufacturing and industrial design, the unsung heroes often lie beneath the surface – quite literally in the case of vacuum press membranes. These critical components play a pivotal role in shaping and refining a multitude of products that we encounter daily, from the sleek curves of a car’s dashboard to the intricate designs of laminated furniture. These rubber membranes are at the heart of numerous transformative processes.
The quality membranes possess remarkable versatility and adaptability, making them indispensable across a wide range of industries. With the ability to cater to different shapes and sizes, they guarantee the highest standards of precision and quality in end products. Whether it’s in woodworking, thermoplastics, or cutting-edge fields like aerospace and automotive, they are crucial parts of the vacuum forming applications.
The unique ability of these materials lies in their capacity to distribute pressure and heat evenly, resulting in flawless adhesion and molding for vacuum pressing. The outcome? Products that boast both aesthetic appeal and durability, making them reliable and long-lasting.
So, you may have stumbled upon my webpage on vacuum press membranes, huh? Talk about fate! But wait, there’s more to unravel. Let’s dive deeper into the world of various types, discover their similarities, differences, and even master the art of choosing the perfect one.
Ready for this thrilling adventure? Let’s go!
What Are Vacuum Press Membranes?
Vacuum press membranes are essential components in the vacuum pressing systems, acting as specialized, flexible sheets critical to the process. They play a vital part in establishing a secure seal around objects undergoing molding or lamination in a vacuum press machine, ensuring optimal operational efficiency.
Their strength lies in their exceptional versatility. Capable of molding to the shape of various items, these membranes guarantee an even pressure distribution that is crucial for effective and precise molding or bonding. This versatility is not just about maintaining the quality of the final product, but also about preserving the integrity of the materials in use.
Available in a variety of materials, each membrane type, from latex and natural rubber to silicone and polyurethane, offers distinct characteristics such as resistance to temperature changes, elasticity, and durability. This range of properties enables them to cater to a wide array of industrial needs, spanning sectors like detailed woodworking, the automotive industry, and the production of composite materials. As we delve deeper, we will explore each of these five types of membranes in detail, uncovering their unique qualities and specific applications.
Introduction to Top 5 Types of Vacuum Press Membranes
Embarking on our tour through the wonderland of vacuum press membranes, we present to you the fabulous five: Latex Membranes, Natural Rubber Membranes, Silicone Membranes, Textured Silicone Membranes, and Polyurethane Membranes.
Let’s take a closer look at each of these membranes to understand their distinct qualities and how they’re utilized across various industries.
Latex Membranes
Latex Membranes represent a crucial category in the vacuum membrane family, known for their remarkable elasticity and durability. These membranes are primarily made from liquid latex, which gives them excellent flexibility and strength, making them ideal for a variety of demanding applications.
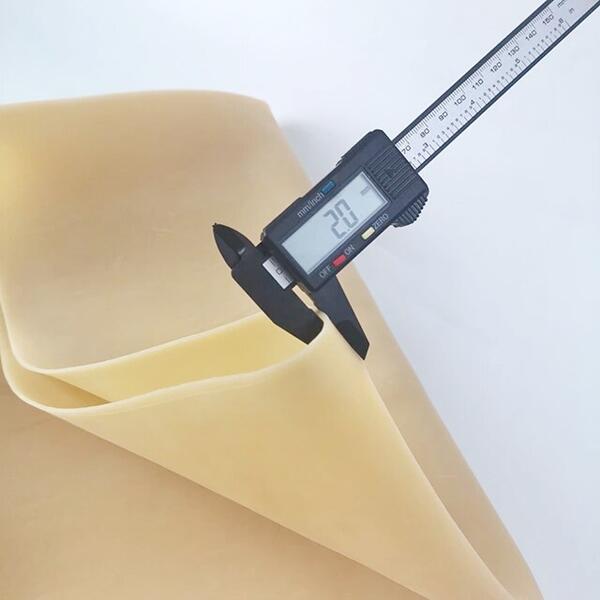
Key Features and Benefits:
- Exceptional Elasticity: Latex membranes can stretch significantly without losing their shape, ensuring a snug and even fit over the materials being processed.
- Durability: They are resilient and can withstand repeated use, making them a cost-effective choice for continuous operations.
- Versatility: Perfect for applications requiring detailed molding, such as intricate woodworking and automotive interior parts.
Ideal Applications:
Latex membranes are predominantly used in industries where detailed and precise molding is required. They excel in woodworking, especially in the production of curved and complex furniture designs. Additionally, they are widely utilized in the automotive industry for components like dashboards and door panels that demand a high degree of precision and durability.
Natural Rubber Membranes
Natural Rubber Membranes stand out for their robustness and adaptability. Crafted from high-quality natural rubber, these membranes offer a perfect balance between flexibility and strength.
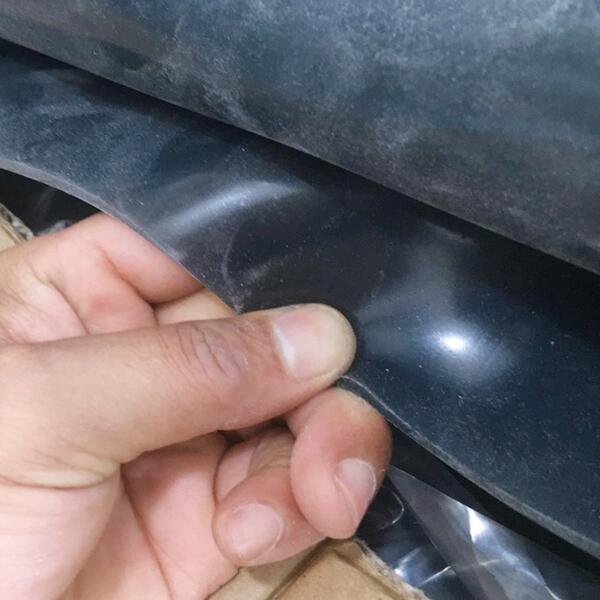
Key Features and Benefits:
- High Elasticity: Ideal for applications that require a membrane to stretch without losing its structural integrity.
- Strong Resistance: These membranes are resistant to wear and tear, ensuring longevity even in demanding environments.
- Adaptability: Their natural composition makes them suitable for a range of applications, including woodworking and lamination.
Ideal Applications:
Natural Rubber Membranes are often the go-to choice for wood lamination and veneering processes. They are also used in applications where detailed, precise molding is essential, such as in creating custom furniture pieces or intricate architectural elements.
Silicone Membranes
Silicone Membranes are known for their outstanding temperature resistance and durability. These membranes are crafted from high-grade silicone, making them ideal for high-temperature applications.
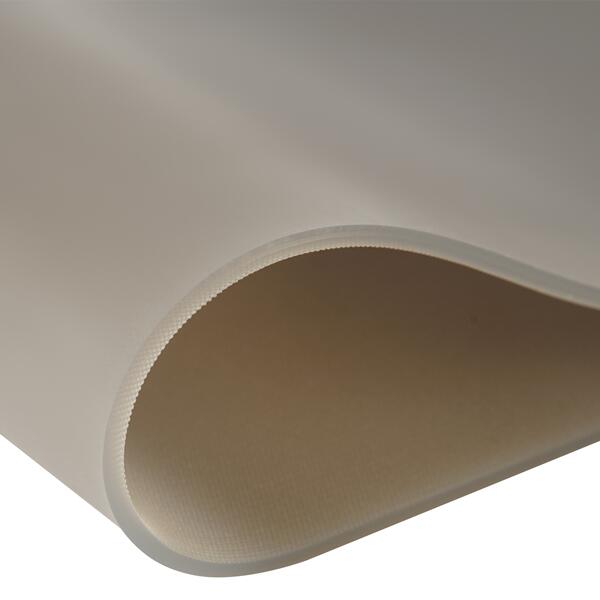
Key Features and Benefits:
- Temperature Resistance: Can withstand extreme temperatures, perfect for applications involving heat.
- Durability: Resistant to chemicals and physical wear, ensuring a long lifespan.
- Flexibility: Maintains flexibility even under high temperature, allowing for precise molding.
Ideal Applications:
These membranes are particularly suitable for thermoforming applications, including the molding of solid surfaces and thermoplastics. Their ability to handle high temperatures makes them perfect for use in aerospace and automotive industries.
Textured Silicone Membranes
Textured Silicone Membranes are a specialized variant, known for their unique surface texture that enhances their functionality.
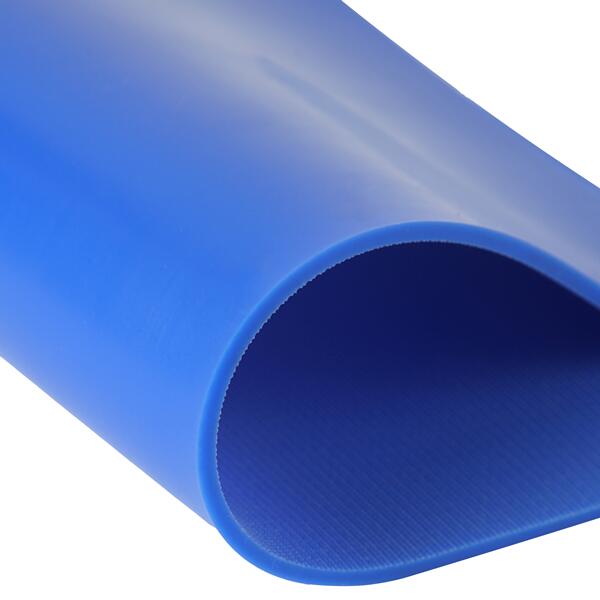
Key Features and Benefits:
- Enhanced Air Evacuation: The textured surface allows for better air evacuation, ensuring a flawless finish.
- High-Temperature Endurance: Inherits the temperature-resistant qualities of silicone, making it suitable for demanding applications.
- Versatile Use: The texture adds an extra layer of functionality, ideal for detailed and precise applications.
Ideal Applications:
These membranes are often used in sophisticated vacuum forming processes where the texture aids in creating detailed and complex shapes. They are a preferred choice in industries where precision and a flawless finish are crucial.
Polyurethane Membranes
Polyurethane Membranes are celebrated for their cost-effectiveness and versatility. Made from high-quality polyurethane, these membranes offer a great balance of performance and affordability.
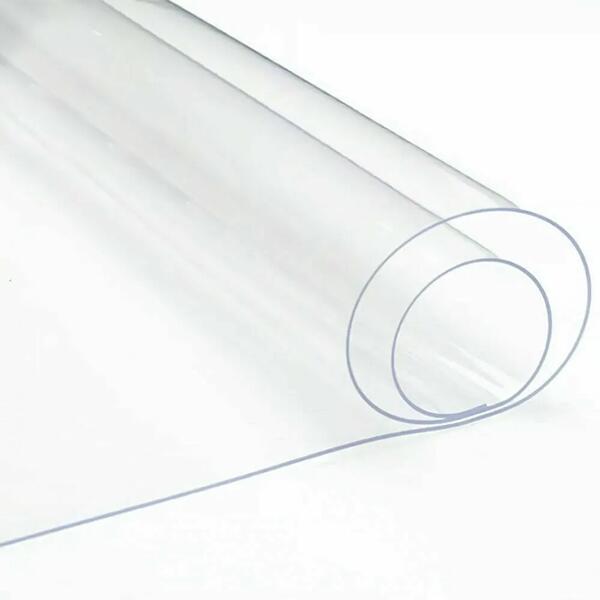
Key Features and Benefits:
- Budget-Friendly: Offer a cost-effective solution without compromising on quality.
- Flexibility and Strength: Provide a good balance between flexibility and tensile strength.
- Wide Range of Applications: Versatile enough to be used in various industrial processes.
Ideal Applications:
Polyurethane membranes are commonly used in veneering, laminating, and bending applications. Their affordability and versatility make them a popular choice for small businesses and diverse industries, including furniture manufacturing and interior design.
Updated Comparison Table Sheet of Top 5 Vacuum Press Membranes
To help you make sense of these diverse membranes and their individual strengths, we’ve crafted a savvy comparison table. This table breaks down the key traits and typical uses of each membrane type, making it a breeze to determine which one perfectly matches your requirements.
Table follows here:
Feature/Type | Latex Membranes | Natural Rubber Membranes | Silicone Membranes | Textured Silicone Membranes | Polyurethane Membranes |
Primary Uses | Woodworking & automotive industries | Woodworking vacuum presses & wood lamination machines | Vacuum forming Solid Surfaces & thermoplastics | Vacuum forming Solid Surfaces & thermoplastics | Vacuum bagging technique, veneering, laminating & curving wood |
Characteristics | Exceptional elasticity & toughness | High elasticity, temperature resistance & durability | High temperature resistance & elasticity | High temperature resistance & textured finish | Supreme durability, clear transparent finish |
Thickness | 2 mm | 2 mm | 1/2/3 mm | 2/3 mm | 0.5 mm |
Width | 1800/2000 mm | 1540 mm | 1400/1800/2000 mm | 1650mm (2000 mm available on request) | 1600mm |
Hardness (Shore A) | 43 | 45 | 45 | 50 | 87 |
Elongation | 650% | 650% | 860% | 500% | 450% |
Tear Strength | 30 N/mm | 30 N/mm | 45 N/mm | 32 N/mm | 60 N/mm |
Working Temperature Range | -40 to 80 ºC | -40 to 110 ºC | -60 to 250 ºC | Up to 250 ºC | Up to 50 ºC |
Color | Caramel (Natural) | Grey | Grey Trans | Blue | Transparent |
Surface Finish | Smooth (textured on request) | Smooth | Smooth | Textured on one side | Smooth |
Notes:
Product specifications may vary by manufacturer. For detailed technical information, please contact the supplier directly.
Applications of Vacuum Press Membranes
Vacuum presses membranes have a broad range of applications across multiple industries, showcasing their versatility and importance in modern manufacturing processes. Here are some key sectors where these membranes are extensively used:
Woodworking Industry
- Bent Laminations and Form Veneering: For vacuum pressing curved laminated shapes with various materials.
- Flat Pressing of Panels, Veneers, and Laminates: Suitable for creating wooden panels with veneers, decorative laminates, and high-gloss materials.
- Gluing Panels and Solid Wood Edges: For pressing panels and gluing solid timber edges without clamps.
- Veneering Profiles: For gluing veneers to 2D shaped profiles.
- High-Strength Bonding: Using heat-activated adhesive and resins for pressing veneers and laminates.
Solid Surface Industry
- Preheating and Vacuum Forming Solid Surface Materials: For materials used in bathrooms, kitchens, and furniture, as well as designs in restaurants, hotels, and more.
- Hydraulic Pressing: For deep and complicated 3D shapes with tight radiuses, using hydraulic presses with male/female molds.
- Vacuum Pressing: For preheated material placed onto a mold inside the vacuum former.
Thermofoil Industry
- Three-Dimensional Thermofoil Lamination: For routed MDF panels, like kitchen fronts, cabinets, and furniture.
- Two-Dimensional Thermofoil Lamination: For pre-shaped profiles, such as door profiles, wood moldings.
Thermoplastic Industry
- 3D Plastic Sheet Vacuum Forming: For creating items like protective housing, casings, decorative panels, and printed PETG.
- 2D Plastic Vacuum Forming: For thermoforming simple shapes like edge guards, windshields, door moldings, profiles.
Automotive Industry
- Production of Car Dashboards, Side Panels, Covers, and Wood Trims: Used for wrapping and covering components like dashboards and armrests with leather or fabrics, and veneering interior wood trims and panels.
- Three-Dimensional Covering and Pressing of Dashboards: Particularly with leather or artificial leather.
- Wood Veneering of Car Panels and Trims: For high-strength veneering of interior panels and trims with natural wood veneers.
- Laminating Car Side Panels and Covers: Covering side panels and covers with leather or fabrics.
Composite Industry
- Pressing and Vacuum Forming of Composite Materials: For fabrics and fiber materials, using sophisticated vacuum presses with infrared heating systems.
- Hot Vacuum Pressing of Multiple Layers: Used for multiple layer pressing with heat application for various fabric materials, like carbon or glass fibers.
- Vacuum Forming of Composite Materials: Thermoforming and vacuum forming of composite materials, such as multiple layer fabrics and wood-plastic composites
Sublimation Industry
- Large-Format Sublimation of Hard Substrates: For materials like aluminium, glass, acrylic glass, HPL, and wood.
- Sublimation and Thermoforming: For Solid Surface, plastics, acrylic materials.
- 3D Sublimation of Hard Substrates: On pre-shaped 3D objects, such as shower plates made out of resins, and shelves made out of aluminium or other metals.
Each of these applications showcases the versatility and critical role of vacuum forming membranes in various manufacturing and production processes across multiple industries.
Choosing the Right Membrane for Your Application
When choosing the perfect membrane sheet that aligns with your requirements, it is crucial to take into account the intended use as well as budget constraints. With different types available—such as latex, natural rubber, silicone, textured silicone, and polyurethane—each membrane brings its distinct properties, making them replaceable for a wide range of applications.
Assessing Application Requirements:
Understanding the demands of your specific application is the crucial first step. Different membrane types offer varying levels of temperature resistance, durability, and flexibility. For high-temperature processes, silicone membranes are the go-to choice due to their excellent heat resistance. On the other hand, if flexibility and elasticity are your primary concerns, consider latex or natural rubber membranes. These options provide engaging solutions tailored to your needs.
Balancing Quality with Budget:
Budget considerations are equally important. While some membranes boast advanced features, they may also carry a higher price tag. Weighing the cost against the benefits and performance of each membrane type is essential to finding the most cost-effective solution for your needs.
Why Consider DeerHunter’s Silicone Membranes?
At Deer Hunter, while we offer a range of membrane options, we have a particular inclination towards our silicone membranes. They are versatile, high-performing, and epitomize the quality and dependability our brand is known for. We recognize that every client has unique needs, and our recommendation is tailored with a deep respect for your specific project requirements and preferences.
Our Commitment to Your Success:
To demonstrate our confidence in our silicone membranes, we are pleased to offer complimentary samples to all our clients, irrespective of their location, with all shipping expenses covered by us. This gesture is a testament to our commitment to client satisfaction and our desire to provide you with all necessary resources to make an informed decision.
No matter which type of membrane you choose, our team at Deer Hunter is dedicated to delivering exceptional products and support throughout your journey with us.
Benefits of Choosing Our Silicone Membranes
Ready to level up your game? Look no further than Deer Hunter’s silicone membranes. With a variety of advantages and bonuses, we’re here to show you what exceptional quality and customer service are all about. Brace yourself for the key benefits:
- Superior Quality Assurance: Our silicone membranes are produced with the highest standards of material quality and manufacturing excellence, ensuring they perform consistently and reliably in various applications.
- Enhanced Durability: Designed to withstand extreme temperatures and rigorous use, our membranes offer longevity, reducing the need for frequent replacements and thereby lowering long-term costs.
- Versatility in Applications: Our silicone membranes are suitable for a wide range of applications, from woodworking and automotive to aerospace and thermoplastics, providing flexibility and utility.
- Customization Options: Understanding that each project has unique requirements, we offer customization options for our silicone membranes, ensuring they meet your specific needs in terms of size, thickness, and other parameters.
- Exceptional Customer Service: Our team is dedicated to providing comprehensive support, from assisting with initial inquiries to offering post-purchase assistance, ensuring a seamless experience for all our clients.
- Technical Support and Guidance: We provide expert technical support and guidance to help you make the most of our membranes, ensuring optimal usage and performance in your specific applications.
- Fast and Reliable Delivery: Recognizing the importance of timely operations, we ensure fast and reliable delivery of our membranes, so your projects are not delayed.
- Competitive Pricing: Despite the premium quality, our silicone membranes are offered at competitive prices, striking the right balance between quality and affordability.
- Eco-Friendly Options: Committed to sustainability, we also offer eco-friendly silicone membrane options, catering to environmentally conscious businesses.
By choosing our silicone membranes, you not only receive a product of unmatched quality but also become a part of our extended family, where your satisfaction and success are our top priorities.
The Procurement Process of Vacuum Membranes
To ensure a smooth and efficient purchasing experience, we have streamlined our procurement process for silicone membranes. Here’s a step-by-step guide to simplify your journey from inquiry to acquisition:
- Initial Inquiry: Reach out to us through our website, email, or phone to express your interest in our silicone vacuum membranes. Our team is ready to assist you with any initial queries you may have.
- Consultation and Requirements Gathering: We engage in a detailed consultation to understand your specific needs, including the size, thickness, and application of the membranes.
- Customization and Quotation: Based on your requirements, we provide options for customization. A detailed quotation including pricing, delivery timelines, and terms is then prepared for your review.
- Sample Evaluation: If requested, we can provide samples of our silicone membranes for your assessment. This step ensures that our product meets your expectations and requirements.
- Order Confirmation and Payment: Once you are satisfied with the sample and quotation, you can confirm the order and proceed with the payment through our secure payment channels.
- Production and Quality Assurance: Upon order confirmation, we begin the production of your silicone membranes. Our quality assurance team ensures that every membrane meets our high-quality standards.
- Shipping and Delivery: After production, your order is carefully packaged and shipped. We provide tracking information and ensure timely delivery as per the agreed schedule.
- Post-Delivery Support: After you receive your order, our customer service team remains available for any post-purchase support, including assistance with installation, usage, or any queries.
- Feedback and Continuous Engagement: We value your feedback and encourage you to share your experience. Our team is committed to maintaining a relationship for ongoing support and future needs.
This straightforward process is designed to ensure that acquiring our silicone membranes is as effortless and satisfying as using them in your applications.
Frequently Asked Questions
Q1: What are the primary advantages of using silicone membranes in vacuum pressing?
A1: Silicone membranes are favored for their excellent heat resistance and durability, making them ideal for high-temperature applications. They are also highly flexible and resistant to chemicals, ensuring longevity and consistent performance in various industrial processes.
Q2: Can silicone membranes be customized to specific sizes or thicknesses?
A2: Yes, we offer customization options for our silicone membranes. Clients can request specific sizes, thicknesses, and even certain physical properties to meet their unique application requirements.
Q3: How do silicone membranes compare to other types of membranes in terms of cost?
A3: While silicone membranes may have a higher upfront cost compared to some other types, their durability and versatility often result in a lower total cost of ownership. They are a cost-effective choice in the long run, especially for processes involving high temperatures or chemical exposure.
Q4: Are silicone membranes environmentally friendly?
A4: We are committed to sustainability, and our silicone membranes are designed to be eco-friendly. They are durable, reducing the need for frequent replacements, and are made from materials that are less harmful to the environment.
Q5: What support does Deer Hunter offer post-purchase of silicone membranes?
A5: After purchasing our silicone membranes, clients can expect comprehensive support that includes technical guidance for optimal use, assistance with any installation queries, and responsive customer service for any post-purchase questions or concerns.
Q6: How long do vacuum press membranes typically last?
A6: The lifespan of a vacuum press membrane depends on the material type, usage frequency, and application conditions. Generally, with proper care and under normal usage conditions, a vacuum membrane can last several years.
Q7: Can vacuum press membranes be used for both hot and cold pressing applications?
A7: Yes, most vacuum press membranes are suitable for both hot and cold pressing applications. However, it’s important to choose a membrane material that best suits the temperature requirements of your specific process.
Q8: Are there any maintenance tips to prolong the life of vacuum press membranes?
A8: Regular cleaning and proper storage are key to prolonging the life of your membranes. Avoid sharp objects that can cause tears, and store membranes flat or rolled, not folded, to prevent creases and damage.
Q9: How do I determine the right thickness of a vacuum press membrane for my application?
A9: The thickness needed often depends on the complexity and detail of the items being pressed. Thicker membranes are generally more durable and better for simple shapes, while thinner membranes can conform more closely to intricate designs.
Q10: Is it possible to repair a damaged vacuum press membrane?
A10: Minor damages and punctures in some types of vacuum press membranes can often be repaired with patch kits. However, significant damage might require the membrane to be replaced. Always consult with the manufacturer for the best repair practices.
Q11: What are the best applications for Latex Membranes in vacuum pressing?
A11: Latex Membranes excel in applications requiring high elasticity and resilience. They are ideal for woodworking, particularly in creating curved and complex shapes, and are also used in automotive applications for flexible yet durable parts.
Q12: How do Natural Rubber Membranes perform under repeated use?
A12: Natural Rubber Membranes are known for their durability and resistance to wear and tear. This makes them suitable for continuous use in applications like wood lamination and veneering, where they maintain performance over time.
Q13: Can Silicone Membranes withstand high-temperature applications?
A13: Yes, Silicone Membranes are highly resistant to extreme temperatures, making them ideal for applications involving high heat, such as thermoforming plastics and solid surface materials.
Q14: What is the advantage of the texture in Textured Silicone Membranes?
A14: The texture in Textured Silicone Membranes enhances air evacuation, leading to better molding results and a higher-quality finish, particularly in detailed vacuum forming applications.
Q15: Are Polyurethane Membranes suitable for large-scale industrial use?
A15: Absolutely. Polyurethane Membranes are both versatile and cost-effective, making them a suitable choice for a wide range of industrial applications, including large-scale veneering and lamination processes.
Exclusive Offer: Unlock Your Reader Rewards
As a token of our appreciation for your interest and engagement, we are excited to offer an exclusive bonus for readers who reach out to us with inquiries. Here’s how you can unlock your special reader rewards:
- Special Code for Recognition: When you send us an inquiry, simply include the code “007” in your message. This will let us know that you have come to us through this article, allowing us to extend these special offers to you.
- Complimentary Samples: We understand the importance of experiencing product quality first-hand. As part of this exclusive offer, we will provide free samples of our vacuum press membranes, with all shipping costs covered by us.
- Discount on Orders: To further show our gratitude, we are offering a 5% discount on all orders placed by readers of this article. This is our way of saying thank you and helping you make the most of your procurement.
These exclusive reader rewards are our way of acknowledging the value we place on informed clients like you. We believe that an informed decision is a wise decision, and we’re here to support you every step of the way in making the best choices for your business needs.
Closing Insights
In summary, the right vacuum press membrane can significantly elevate your project’s quality and efficiency. Whether it’s Latex, Natural Rubber, Silicone, Textured Silicone, or Polyurethane, each option holds the key to unlocking new possibilities in manufacturing.
As you consider your next steps, remember that Deer Hunter is here to assist. For more information, guidance, or to discuss your specific needs, don’t hesitate to reach out to us. Contact us at sales@cndeerhunter.com, or visit our website for more details.
Thank you for exploring the world of vacuum press membranes with us. We’re excited to help you find the perfect solution for your manufacturing needs.