Nowadays, as the demand for glass products rises, laminated glass is also regularly seen in modern architecture and construction, offering numerous benefits such as safety, UV blocking, and sound insulation. In order to get high grade laminated safety glass, how to make better use of silicon vacuum bags in glass lamination ovens is becoming increasingly important.
In this blog, I’m going to provide an in-depth explanation of these components, their connections and their functions in the glass manufacturing industry.
Here we go!
What is Laminated Glass?
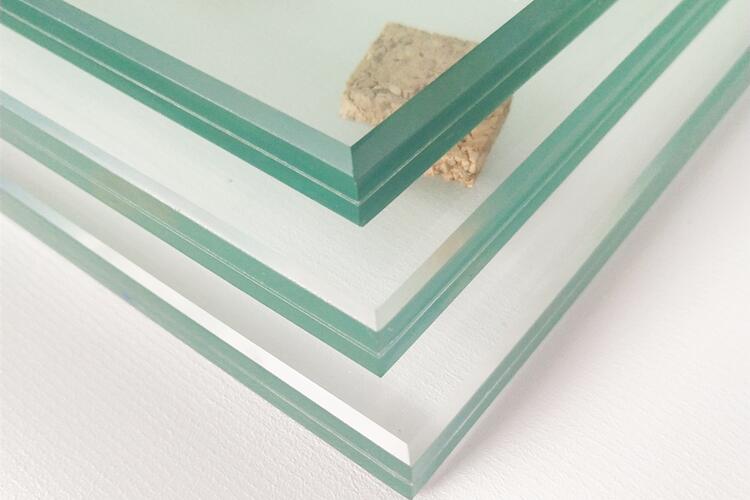
Definition
Laminated glass is a type of safety glass that is made by sandwiching a thin polymer interlayer, typically of polyvinyl butyral (PVB), ethylene-vinyl acetate (EVA) between two or more panes of glass at high temperature and pressure using an oven. The multiple layers are then heated and pressed together to form a single sheet of glass.
Simply Put:
Laminated glass is made by bonding two pieces of glass together with a sheet of plastic in the middle. You heat up this little sandwich and press everything together, and the plastic melts and sticks to the glass.
It’s pretty easy to tell whether glass has truly been laminated. By viewing it on edge, you’ll see a visible interlayer.
Compared to tempered glass, laminated glass is designed to remain intact upon breakage, as the broken pieces adhere to a layer of plastic within the glass rather than dispersing into fragments. This ensures increased safety, as the shattered glass remains contained within the frame rather than posing a hazard by scattering onto the floor.
Benefits
1: Laminated glass is an excellent choice for those who want to maximize security. It is resistant to impact, shatter, and penetration, making it suitable for high-risk environments.
2: Enhance UV protection or screening capabilities.
3: Provide soundproofing for your home by installing laminated glass windows.
4: The interlayers in laminated glass can be used to achieve transparency or tinting effects.
Applications
1: The most common use of laminated glass is for architecture, skylight glazing, automobile safety windshields, photovoltaic, UV protection, and artistic expression.
2: In geographical areas requiring hurricane-resistant construction, laminated glass is often used in exterior storefronts, curtain walls, and windows.
Common materials used as interlayers
Laminated glass gets its name from its construction, which consists of multiple layers of glass with an interlayer sandwiched between them. The interlayer, which is placed between the glass layers, is typically made of EVA, PVB, or SGP materials.
EVA
EVA, short for Ethylene Vinyl Acetate, is an alternative interlayer for safety glass that offers unique advantages. EVA is highly resistant to moisture and can be used in both internal and external glazed applications with exposed edges. It also adheres better to glass and other materials than PVB and comes in a variety of colors, making it a great choice for design-oriented projects.
EVA allows for the combination of various materials such as fabrics, paper, decorative wire mesh, printed PET films, and even photovoltaic cells (solar panels) in the glass build-up, resulting in distinctive and innovative products.
PVB
Poly Vinyl Butyral is a tough plastic resin that is used in between two panes of glass to bond them together. It’s made from polyvinyl alcohol through reacting it with butyraldehyde.
PVB, or polyvinyl butyral, is a popular interlayer material used in the production of laminated glass worldwide. Its widespread use is due to its excellent optical clarity, flexibility, and strong adhesion to various surfaces. PVB is commonly used in the manufacturing of laminated glass for architectural and automotive applications, making it a go-to choice for glass manufacturers.
SGP
SGP is called the ionic interlayer film (SentryGlas Plus), which is a high-performance interlayer developed by DuPont.
SGP is 100 times more rigid and 5 times more resistant to tearing when comparing to PVB.
Leading manufacturers
FORMS AND SURFACES INDIA PVT LTD.
Steps for producing laminated glass
1: Cut the glass to the desired size and shape.
2: Clean the glass surfaces thoroughly to remove any dirt or debris.
3: Put one or more layers of PVB or EVA interlayer between the glass layers.
4: Insert the glass panes into the silicon vacuum bag, ensuring that the interlayer is properly positioned and there are no wrinkles or air pockets.
5: Seal the bag with the E-seals or U-seals, and make sure the seal is tight and secure.
6: Push the sealed bag into the glass laminating oven.
7: Apply heat and pressure according to the machine’s instructions, allowing the interlayer to melt and bond the glass layers together.
8: Monitor the temperature and pressure to ensure they are maintained properly throughout the glass lamination process.
9: Once the laminating process is complete, remove the silicon bag from the oven and allow it to cool.
10: Inspect the formed laminated glass for quality and guarantee it meets the requested specifications.
It is obvious that the use of a silicon vacuum bag is essential and plays a critical role in the process.
Or you can check below video to learn more:
SO?
What are Silicon Vacuum Bags?
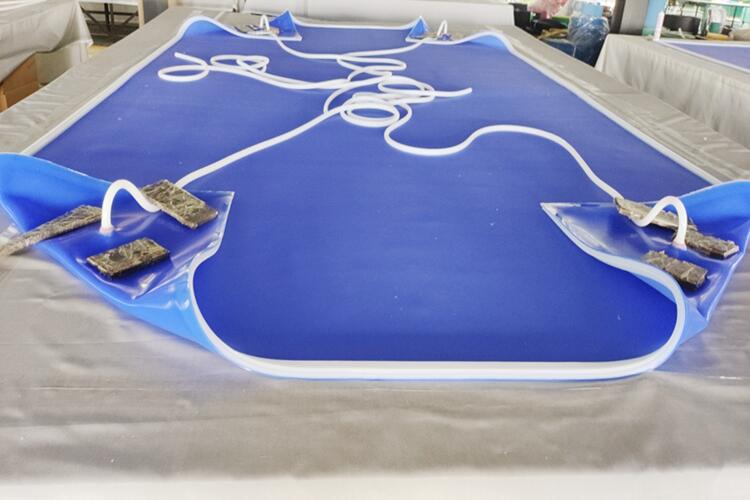
Definition
A silicon vacuum bag is a vital tool used in the manufacture of laminated glass. By removing the air inside the bag after heating, a vacuum chamber is formed which ensures that no bubbles are generated between the glass. This is important because it helps to create a strong bond between two or more pieces of glass.
Under vacuum pressure, the bag compresses the glass, and the adhesive films(EVA/PVB/SGP) between the glass are melted at a high temperature, resulting in final laminated glass that is safe, strong, waterproof, and explosion-proof. This process is achieved without the need for an autoclave, making it a cost-effective and efficient method for producing laminated glass.
Target audience:
1: Manufacturers of laminated glass or safety glass, who have their own factories, technical personnel, and laminating furnaces for producing this type of glass.
2: Glass laminating oven manufacturers, who purchase silicon vacuum bags for sale matching with their production equipment.
3: Equipment intermediaries and rubber product wholesalers/retailers, who purchase vacuum silicon bags and sell them to the local laminated glass manufacturers in their own country.
Technical Data:
Material | Made of 100% silicone rubber |
Common Color | Transparent and Blue |
Surface Finish | Smooth/Textured |
Density | 1.25 ± 0.05g/cm3 |
Hardness | 50 ± 5 Shore A |
Tensile Strength | 9.5MPa |
Tear Strength | 32N/mm |
Max. Temperature | 250°C (482° F) |
Elongation at Tear | 650% |
Compression Set | ≤8% |
Resilience | 30% |
* The above data is obtained from China Deer Hunter. You can also refer to https://cndeerhunter.com/silicone-vacuum-bag-for-laminated-glass to learn more.
Types
1: If you distinguish it by shape, there are E and U-seals silicon bags.
![]() | ![]() |
E-Seals Silicon Vacuum Bags | U-Seals Silicon Vacuum Bags |
- U-seal silicon vacuum bags are a specialized type of vacuum bag that features a unique U-shaped sealing bar at the two layers of the bag. This innovative design provides a more secure seal and even pressure distribution during the vacuum process, making it ideal for use in industries such as aerospace, automotive, and glass laminating. With U-seals bags, manufacturers can produce high-quality laminated products with ease and efficiency.
- E-seal silicon vacuum bags are a type of vacuum bag used in the production of laminated glass. Unlike U-seals, E-seals feature a more sophisticated design in the shape of an “E” that creates a stronger seal around the edges of the bag. This design reduces the risk of air leaks during the vacuuming process and ensures that the bag maintains a tight seal throughout the entire process of glass lamination. E-seals are commonly used in the production of larger-sized laminated glass due to their increased strength and durability.
In order to clarify the two types of bags, you can open this link https://cndeerhunter.com/u-seals-silicone-vacuum-bags
2: The colors available include transparent, blue, red, green, and others.
It’s important to note that the color of the bag does not affect its quality. Typically, transparent and blue are the most popular color choices, while red and green are less commonly requested by customers.
Benefits
1: Provides strong adhesion
Silicone vacuum bags are a reliable solution for laminated glass bonding. By creating a strong adhesion between the layers of glass, these bags ensure that the laminated glass is highly durable and less susceptible to damage. This makes them an ideal choice for applications where safety and strength are of utmost importance.
2: Ensures consistent quality
A popular tool in the production of laminated glass due to their ability to maintain consistent quality. By providing uniform pressure and heat distribution during the lamination process, these bags ensure that the final product is of high quality every time. This has made them a go-to choice for manufacturers looking to produce reliable and consistent laminated glass products.
3: Saves time and money
Silicone vacuum bags are a sustainable option for those looking to reduce waste. Not only are they reusable, but they can also be easily cleaned and resealed for future use. This not only saves money in the long run, but also reduces the need for frequent replacements. Moreover, the use of silicone vacuum bags can significantly speed up the lamination process, resulting in increased productivity and shorter production time.
4: Increases safety
The use of silicone vacuum bags in laminated glass production enhances the safety of the final product. This is because the bags prevent air pockets and other defects that can compromise the strength and durability of the laminated glass.
5: Offers versatility
Manufacturers of laminated glass can benefit from the versatility and cost savings provided by silicone vacuum bags. These bags are capable of accommodating curved and custom shapes, making them an ideal tool for a variety of laminated glass applications. With the use of silicone vacuum bags, glass manufacturers can streamline their production processes and achieve greater flexibility in their operations.
Do you have standard size vac bags?
It is a very common question. However, absolutely not in our workshop.
For customers firstly give us their external sizes of the bags they want, or we give them suggested outer dimensions according to their max glass width and length.
What is your standard configuration for a bag?
Below is an example drawing of a silicon vacuum bag with external size 2540mm X 3760mm X 3mm.
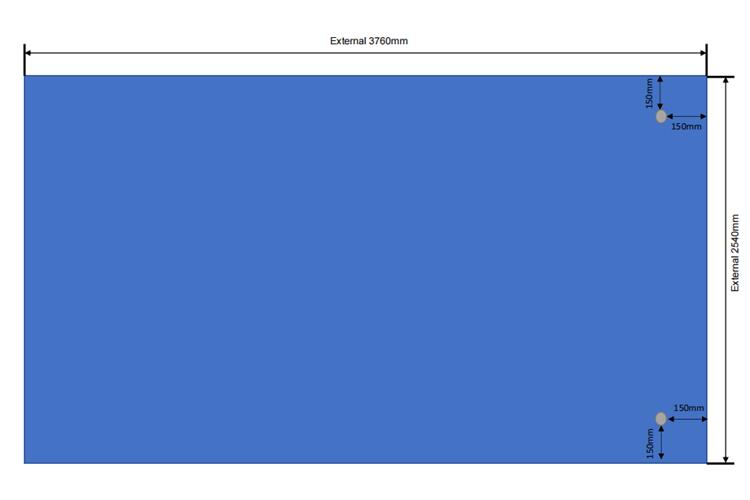
- E seals on the edges
- Two silicone nozzles on the short side.
- Inner diameter (ID) – 6mm and Outer diameter (OD) – 12mm.
- Two silicone hoses, 3M long each hose.
Thickness 3mm or 2mm?
1: Standard thickness in our factory is 3mm. If you want THK 2mm silicon bag, I’m afraid the bag will be more easily worn and torn.
2: Generally, there is no MOQ limit for THK 3mm, but 5-10 sets for THK 2mm. For THK 2mm silicone blankets are not in stock.
How can you protect the bag from being cut by the glass?
To prevent the bag from being cut by the glass during the laminating process, it is recommended to use Teflon open mesh. The material serves as a barrier between the glass and the bag, reducing the risk of the glass puncturing or cutting through the bag.
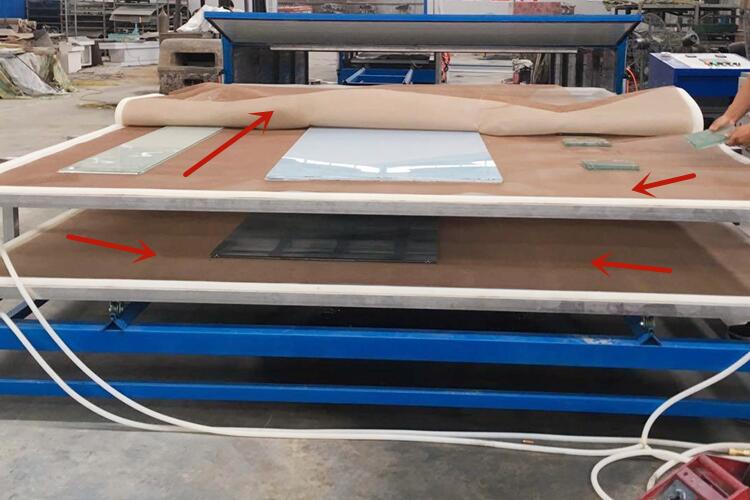
Additionally, it is important to carefully inspect the glass for any sharp edges or protrusions before placing it in the bag. Any sharp edges should be sanded or smoothed down to prevent damage to the bag.
When you read here, it seems that we haven’t explored the machine. Now, it’s time.
What is a Glass Lamination Oven?
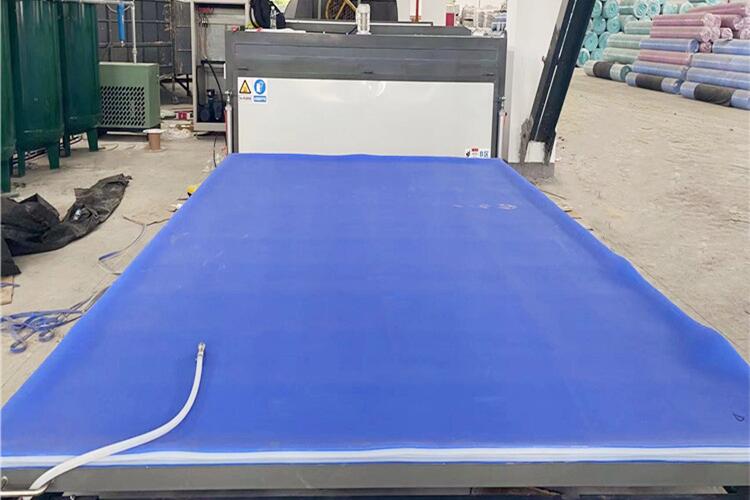
Definition
The glass lamination oven is a specialized equipment used for producing laminated glass. It works by using high temperature and pressure to melt and bond EVA or PVB adhesive films between two or more pieces of glass, resulting in laminated glass with high strength, waterproofing, and explosion-proof properties.
Glass laminating ovens come in different sizes and shapes to suit various glass products. They are also available in different heating methods such as convection and infrared heating.
Application
This equipment is suitable for glass processing factories and can produce various types of laminated glass. Its features include easy operation, low energy consumption, and high efficiency, without the need for a high-pressure autoclave.
Leading manufacturers
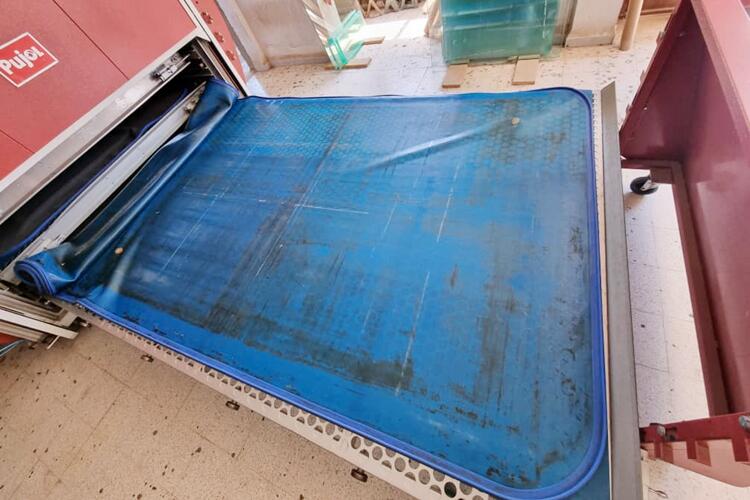
Pujol Group
Steps for starting glass laminating ovens
By following these steps, a glass laminating oven can be properly prepared for operation, helping to ensure a successful and efficient production process.
1: Cleaning
Thoroughly clean the oven, including the heating elements, rollers, and any other surfaces that come into contact with the glass.
2: Preheating
Set the oven to the desired temperature and allow it to preheat for the recommended amount of time.
3: Loading the glass
Place the glass into the silicone vacuum bag, making sure it is properly positioned and any necessary interlayers or films are in place.
4: Sealing the bag
Seal the silicone vacuum bag with the appropriate sealing equipment, ensuring a tight seal around the glass.
5: Loading the bag
Load the sealed silicone vacuum bag into the oven, taking care not to damage the bag or its contents.
6: Vacuuming
Use a vacuum pump to remove the air from the bag, creating a vacuum environment for the glass to cure.
7: Heating
Begin the heating cycle, which should be carried out according to the specifications of the glass and any interlayers or films used.
Conclusion and Final Thoughts
If are getting stuck in searching for a reliable and cost-effective way to laminate your glass products?
Look no further than resuable silicon vacuum bags! These innovative bags offer a number of benefits over traditional laminating methods, including improved efficiency, enhanced clarity, and increased durability.
Whether you’re a professional glass fabricator or a DIY enthusiast, this guide is the perfect resource for learning how to use these bags to achieve stunning results. From choosing the right materials and tools to understanding the laminating process and troubleshooting common issues, our guide is packed with expert tips and advice to help you get the most out of your silicon vacuum bags.
So why wait? Discover the power of silicon vacuum bags today and take your glass laminating project to the next level.
Now, It’s your turn.
For more information, please send messages according to the right table, or contact us via your sales associate, our contact form, our mobile/WhatsApp number +86-13823789007, or email us at sales@cndeerhunter.com