In the world of manufacturing, 3D lamination has revolutionized the way we create stunning and durable surfaces. However, the success of this technique relies heavily on a hidden hero – silicone membranes. These flexible and heat-resistant materials play a key role in ensuring the perfect finish for 3D laminated components.
Silicone membranes are essential for achieving seamless results in the lamination process. They act as a protective barrier, preventing any air bubbles or imperfections from appearing on the surface. By evenly distributing pressure and heat, these membrane sheets ensure that the adhesive bonds perfectly with the substrate, resulting in a flawless finish.
Choosing the right silicon sheet is crucial for achieving consistent and high-quality results. Factors such as thickness, durometer, surface finish, and tear resistance are all important considerations when selecting the appropriate silicone rubber membrane for a specific application.
In this article, we will dive deeper into the world of silicone membranes and uncover their secrets to successful 3D laminate. From the various types of diaphragmss available to expert tips for optimal usage, we will provide you with valuable insights that will enhance your lamination process and take your creations to the next level.
Why choose 3D lamination?
3D lamination represents a revolutionary approach to surfacing that eliminates the need for edge banding or T-molding, ensuring seamless, edge-to-edge perfection. It’s particularly advantageous for non-flat or intricately contoured surfaces where traditional lamination falls short. With 3D lamination, you can achieve visually stunning aesthetics reminiscent of wood and other materials, all while enjoying exceptional durability and cost-effectiveness.
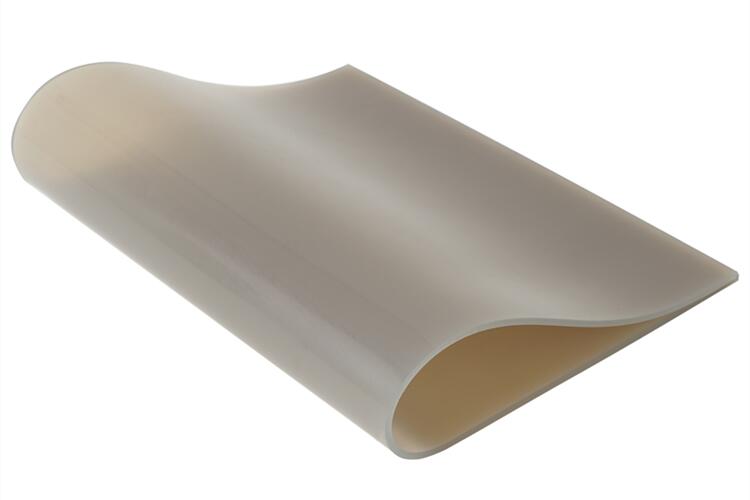
Benefits of 3D lamination:
(1) Unmatched flexibility in design.
(2) Remarkable affordability, making it accessible for a wide range of applications.
(3) Impenetrable water resistance.
(4) Immunity to mold growth.
(5) Effortless maintenance and cleaning.
(6) Exceptional durability that ensures longevity.
(7) Versatility for various industrial environments.
The role of silicone membranes in 3D lamination
In 3D lamination, vacuum presses commonly utilize rubber silicone membranes. These membranes serve two primary functions: they speed up heat transfer to the components and exert positive pressure on top of them, while the vacuum underneath provides suction. The advantages include rapid cycle times and the ability to achieve intricate component details in most cases.
However, the membranes may require periodic replacement, depending on the number of cycles and parts produced. Additionally, the initial cost of a membrane press can be substantial, ranging from $20,000 to over $50,000, though you might find more affordable or used options. It’s important to note that not all vacuum presses can operate without the membrane in place.
The most common brands of vacuum presses sold worldwide are Global, Artex, Barth, Orma, Felder, etc. If you are a maker of vacuum presses and do not see your company’s info here please contact us. I apologize if I overlooked it.
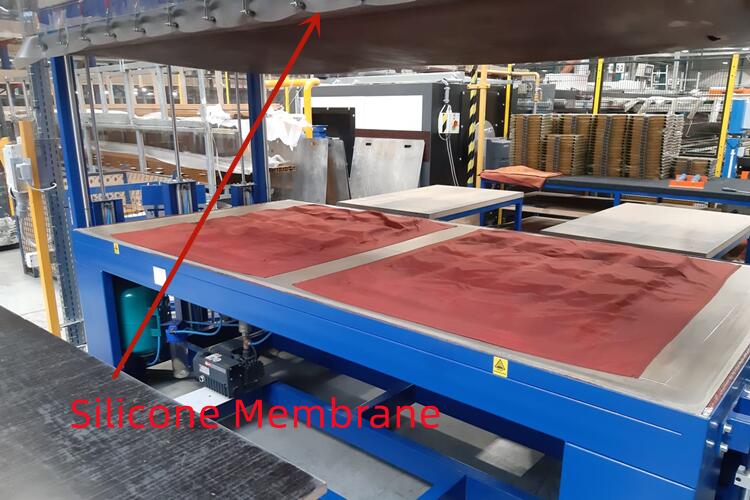
The flexibility and heat resistance of silicone membranes makes them ideal for various vacuum presses. They can withstand high temperatures without deforming, allowing for consistent and uniform pressure distribution during the bonding process. This ensures that the adhesive adheres evenly to the substrate, resulting in a solid and long-lasting bond.
Furthermore, our vacuum membranes are also easy to clean and maintain. Their non-stick properties prevent adhesive residue from sticking to the surface, reducing the need for frequent cleaning and minimizing downtime in production. With proper care, silicone vacuum sheets can be reused multiple times, making them a cost-effective solution for 3DL laminates.
How do silicone membranes work in 3D lamination?
Silicone membranes serve as a shield between the lamination material and the base. They stop air from getting trapped, prevent flaws, and keep the adhesive from spreading out. This leads to a smooth and perfect outcome. Silicone membranes also make sure that pressure and heat are spread evenly, allowing the adhesive to bond effectively with the base, making it sturdy and long-lasting.
During the lamination process, the silicone membrane is placed over the material to be laminated. The vacuum is then applied, which pulls the membrane tightly against the substrate, effectively eliminating any air pockets or imperfections. The heat and pressure applied during the process activate the adhesive and bond it securely to the substrate, creating a seamless finish.
Silicone membranes also provide a level of protection for the material being laminated. They prevent direct contact between the material and the heating element or press, reducing the risk of damage or discolouration. This is especially important for delicate or heat-sensitive materials, ensuring that they retain their integrity and appearance throughout the lamination process.
Advantages of using silicone membranes in 3D lamination
Using silicone membranes in 3D lamination offers several advantages that contribute to the overall success and quality of the process. They include:
- Seamless finish: Silicone membranes ensure that the lamination process is free from imperfections, resulting in a seamless finish that enhances the aesthetic appeal of the final product.
- Uniform pressure distribution: By evenly distributing pressure, these membranes eliminate the risk of air bubbles or uneven bonding, ensuring a consistent and strong bond between the lamination material and the substrate.
- Heat resistance: Vacuum-forming sheets can withstand high temperatures without deforming, enabling the lamination process to be carried out at optimal temperature settings, ensuring a successful bond between the materials.
- Easy maintenance: Silicone vacuum membranes are easy to clean and maintain. Their non-stick properties prevent adhesive residue from sticking, reducing downtime in production and allowing for efficient and uninterrupted workflow.
- Cost-effective: With proper care, vacuum press sheets can be reused multiple times, making them a cost-effective solution for 3D lamination. Their durability and longevity contribute to overall cost savings in the long run.
The advantages offered by silicone membranes make them an indispensable tool for manufacturers and designers looking to achieve high-quality and flawless 3D laminated products.
How to choose the right silicone membrane for your project?
When it comes to choosing the right silicone membrane for a specific 3D lamination project, several factors need to be considered. These factors include thickness, durometer, and tear resistance, among others. Let’s take a closer look at some of the different types of silicone membranes commonly used in 3D lamination:
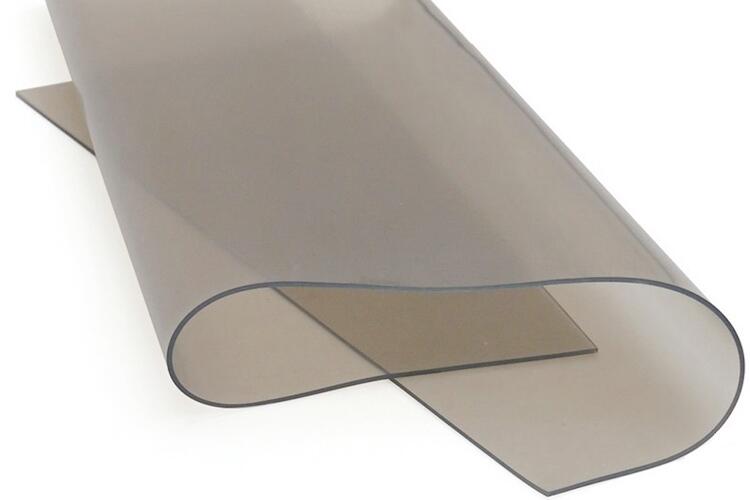
- Thickness: Silicone membranes are available in various thicknesses, ranging from thin to heavy-duty. The thickness of the membrane determines its flexibility and heat resistance. Thinner membranes are more flexible and suitable for intricate or curved surfaces, while thicker membranes offer higher heat resistance and durability, making them ideal for larger or more demanding applications.
- Durometer: Numerous factors influence the application of rubber membranes, with durometer being a critical consideration. Durometer refers to the hardness of the rubber utilized in the membrane. This international standard is determined using a specialized device that creates an indentation in the rubber. Based on its hardness, the membrane is assigned a numerical value, expressed as a whole number ranging from 5 to 100, with a +/- 5 range to account for slight variations. For instance, a membrane with a durometer of 50 actually possesses a hardness falling within the range of 45 to 55. There are three primary types of durometers: Type A, Type D, and Type 00.
- Type A – used for soft rubber
- Type D – used for hard rubber
- Type 00 – used for sponge and foam
- Tear resistance: Tear resistance is an important consideration, especially for applications where the membrane will be subjected to frequent or intense pressure. High tear resistance ensures that the membrane remains intact and can withstand the rigours of the lamination process, resulting in a longer lifespan and enhanced performance.
- Specialized membranes: In addition to standard silicone membranes, there are also specialized membranes available for specific applications. These include anti-static membranes, which prevent static buildup and reduce the risk of damage to sensitive electronic components, and non-marking membranes, which leave no residue or marks on the laminated surface.
Opting for a suitable silicone membrane requires a thoughtful evaluation of the project’s precise demands. By focusing on factors like the ideal thickness, durometer, and tear resistance, manufacturers can secure peak performance and achieve superior outcomes throughout their 3D lamination process.
Tips for using silicone membranes effectively in 3D lamination
Getting the right silicone membrane is crucial for achieving successful 3D lamination. Here are some key factors to consider when selecting the appropriate membrane for your project:
- Application requirements: Assess the specific requirements of your lamination project. Consider factors such as the size and shape of the substrate, the type of material being laminated, and any special considerations or challenges that may arise. This will help determine the ideal thickness, durometer, and tear resistance needed for the silicone membrane.
- Material compatibility: Ensure that the silicone membrane is compatible with the materials being laminated. Some materials may require specific membrane properties, such as heat resistance or anti-static properties, to achieve optimal results. Consult with the silicone membrane manufacturer or supplier to determine the best membrane for your specific materials.
- Quality and durability: Look for silicone membranes that are of high quality and offer durability. Inferior quality membranes may not withstand the demands of the lamination process and may result in subpar results or premature wear and tear. Choose membranes from reputable manufacturers known for their quality and reliability.
- Cost-effectiveness: Consider the cost-effectiveness of the silicone membrane. While high-quality membranes may come with a higher price tag, they often provide better performance and longevity, resulting in cost savings in the long run. Evaluate the overall value and return on investment when making your purchasing decision.
- Expert recommendations: Seek advice from experts or experienced professionals in the field of 3D lamination. They can provide valuable insights and recommendations based on their own experiences and knowledge. Take advantage of their expertise to ensure that you choose the right silicone membrane for your project.
By carefully considering these factors and making informed decisions, you can select the right silicone membrane that will enhance the success and quality of your 3D lamination projects.
Common mistakes to avoid when using silicone membranes in 3D lamination
While silicone membranes offer numerous benefits in 3D lamination, certain mistakes can compromise their effectiveness and the quality of the final product. Avoid the following common mistakes when using silicone membranes:
- Improper membrane selection: Choosing the wrong silicone membrane for the project can lead to subpar results. Ensure that you consider the specific requirements of your project and select the appropriate membrane in terms of thickness, durometer, and tear resistance.
- Inadequate positioning: Improperly positioning the silicone membrane can result in uneven pressure distribution and the formation of air bubbles or imperfections. Take the time to position the membrane correctly, ensuring it covers the entire surface without any wrinkles or folds.
- Incorrect vacuum pressure: Using excessively high or low vacuum pressure can affect the quality of the lamination process. Experiment with different pressure settings to find the optimal balance that ensures proper bonding without causing deformation or incomplete adhesion.
- Inconsistent temperature control: Inconsistent temperature control can lead to uneven bonding or adhesive failure. Maintain the optimal temperature settings throughout the lamination process to achieve consistent and reliable results.
- Neglecting maintenance: Failure to clean and maintain the silicone membrane can result in adhesive residue buildup or damage to the membrane. Follow the manufacturer’s guidelines for cleaning and storage to ensure optimal performance and longevity.
By avoiding these common mistakes, you can ensure that your silicone membranes perform at their best and contribute to the success of your 3D lamination projects.
Case studies: Successful applications of silicone membranes in 3D lamination
To further illustrate the effectiveness of silicone membranes in 3D lamination, let’s take a look at some real-world case studies:
- Furniture industry: In the furniture industry, silicone membranes have been widely adopted for laminating decorative surfaces such as tabletops, cabinet doors, and paneling. The use of silicone membranes ensures a seamless finish, enhancing the overall aesthetics and durability of the furniture.
- Automotive industry: In the automotive industry, silicone membranes are used for laminating interior components such as dashboards, door panels, and trim. The use of silicone membranes ensures a flawless finish, enhancing the visual appeal and longevity of the components.
- Architectural applications: Silicone membranes are also utilized in architectural applications, such as laminating decorative elements for commercial buildings or residential interiors. The use of silicone membranes ensures a high-quality finish, adding visual interest and durability to the architectural designs.
These case studies highlight the versatile applications and benefits of silicone membranes in various industries. By leveraging the power of silicone membranes, manufacturers and designers can achieve superior results in their 3D lamination projects.
Final thought
Are you involved in a project that needs silicone membranes for 3D Lamination?
We’re here to ensure your membrane pressing operations are as efficient as possible. As a trusted partner working with numerous vacuum press manufacturers, Deer Hunter recognizes the significance of quality and enhancing your profitability. This is why we’ve put together this blog post to guide you in maximizing the lifespan of your membranes, whether they are made of silicone or natural rubber.
Deer Hunter offers rubber membranes for use in a wide range of industrial applications. Nowadays we are well-known across industries for creating trusted products and solutions for 3D lamination, manufacturers, and membrane press experts.
The term membrane is also interchangeable with terms like a bladder, sheet or diaphragm. Choose Deer Hunter silicone membranes for all your industrial, manufacturing, and project needs.
Get in touch with us today to discuss your project requirements, and let us assist you in selecting the perfect rubber silicone membrane.
Just send messages to me according to the right table sheet or directly contact me by emailing sales@cndeerhunter.com or via Mobile/Whatsapp/WeChat: +86-13823789007.