Are you looking for the perfect silicone membrane for your vacuum forming machine but feeling overwhelmed by the variety of options? With so many colors, sizes, and thicknesses available, it can be challenging to know where to start.
Don’t worry – you’re in the right place! This article will break down the key factors you need to consider when choosing the ideal silicone membrane sheet for your vacuum press applications.
Keep reading to discover everything you need to know about selecting the right silicone membrane for uses such as foil pressing, glass lamination, solid surface material forming, and composite industries.
Understanding Vacuum Forming Silicone Membrane
Vacuum forming is a thermoforming process that involves shaping a silicone sheet under vacuum pressure to create a mold. This technique is widely used for quickly and easily producing components made from wood, metal, plastic, and other materials, often over a pre-existing mold. It’s especially popular in industries that require rapid prototyping or short-run production of 3D objects.
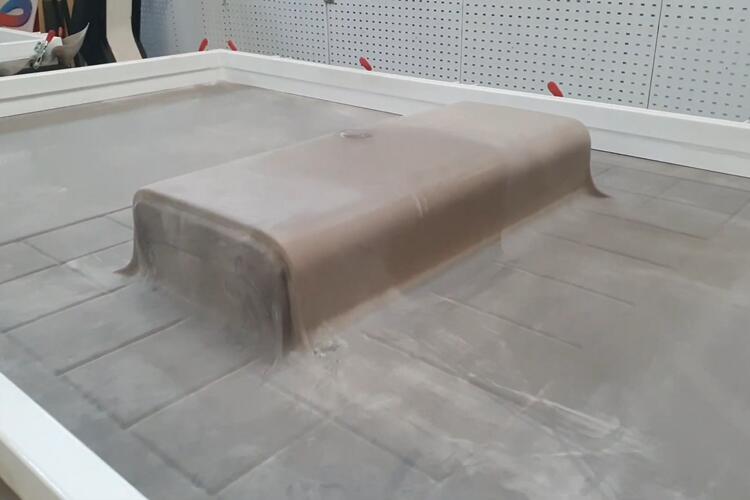
The process begins by placing a pre-formed silicone membrane over the mold. The mold is then placed inside a vacuum forming machine, where vacuum pressure pulls the membrane sheet tightly against the mold. The sheet is subsequently heated until it softens enough to conform to the mold’s shape. Once cooled and hardened, the silicone sheet retains the molded shape, resulting in the finished product.
Thermoforming silicone sheets, commonly referred to as vacuum forming silicone sheets, are known for their exceptional temperature tolerance and high elasticity, making them ideal for both hot press and vacuum forming applications.
Comparing Silicone Membranes and Natural Rubber Membranes
When choosing the right membrane for your vacuum press machine, it’s crucial to understand the differences between silicone membranes and natural rubber membranes. Both types have their advantages, but their suitability depends on the specific requirements of your application, such as temperature tolerance, environmental conditions, and cost considerations. Below is a comparison that highlights the key features of each material.
Comprehensive Comparison
Feature | Silicone Membranes | Natural Rubber Membranes |
Strength & Elasticity | High strength and elasticity. | Superior strength and elasticity. |
Temperature Resistance | Excellent high-temperature resistance up to 250°C. | Suitable for temperatures up to 100-130°C. |
Weather Resistance | Outstanding resistance to extreme weather conditions, including temperature fluctuations, sulfurization, and UV exposure. | Limited resistance to weather extremes, performs best in mild conditions. |
Hydrophobic Properties | Some silicone membranes are hydrophobic, making them ideal for wet or humid environments. | Typically not hydrophobic, less suitable for wet or humid conditions. |
Applications | Highly recommended for laminating PVC foil, wood veneering, bending of wood, MDF, and thermoforming solid surface sheets and thermoplastic materials. | Best suited for indoor applications or mild outdoor conditions. |
Durability | Longer-lasting due to excellent material stability and resistance to wear and tear. | Generally shorter lifespan due to less resistance to UV and extreme temperatures. |
Cost | High cost-performance ratio. | Less expensive, but suitable for limited use conditions. |
Key Takeaways
- Silicone membranes are ideal for a wide range of high-performance applications, offering superior resistance to extreme conditions, higher temperatures, and durability.
- Natural rubber membranes are a more affordable option but are best used in controlled environments with limited exposure to high temperatures, UV, and weather extremes.
Applications of Vacuum Press Membranes
Vacuum press membranes are versatile materials used across various industries for applications such as lamination, decorative element insertion, and creating custom cabinet door skins and furniture panels. They are essential in forming rigid composite materials with precise dimension control, enabling high-strength bonds over large areas. These membranes also help reduce production time while ensuring the overall quality of the finished product.
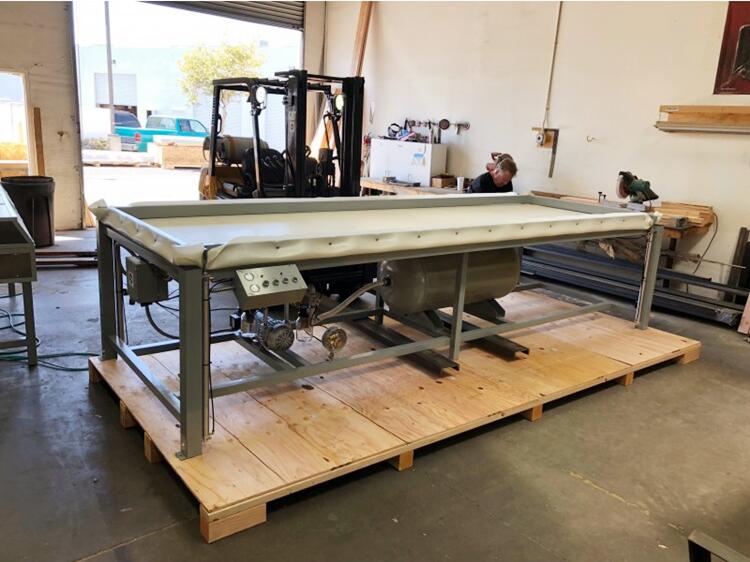
Key Applications of Vacuum Press Membranes
1. Thermoforming
- 2D and 3D vacuum forming of acrylic and thermoplastic materials.
- Production of worktops, sinks, shells, bar counters, bathrooms, window sills, and interior elements.
2. Woodworking
- Veneering and laminating flat and curved solid surfaces.
- 3D foil pressing for PVC.
3. Sublimation
- Tailored advice for 3D and large-format sublimation on a wide variety of hard substrates, including aluminum, acrylic stone, glass, metal sheeting, acrylic sheets (PMMA), textiles, and wood (HPL, MDF, HDF).
Key Benefits of Vacuum Press Membranes
- High-Strength Bonding: Achieves strong, durable bonds across large surfaces with precision.
- Efficiency: Reduces production time, leading to cost savings while maintaining high product quality.
- Versatility: Suitable for a wide range of materials, from acrylic and wood to textiles and metals.
Where to Purchase Silicone Membranes for Your Vacuum Press
If you need a cost-effective and reliable silicone membrane for your vacuum press machine, Deer Hunter offers the perfect solution for your needs.
With years of expertise in production and advanced machinery, we provide silicone sheets in various sizes and thicknesses, ensuring a precise fit for your specific application.
We also offer customized production to meet your quality and quantity requirements. Simply send us your sample, and we’ll take care of the rest.
Here’s what our customers are saying about our products:
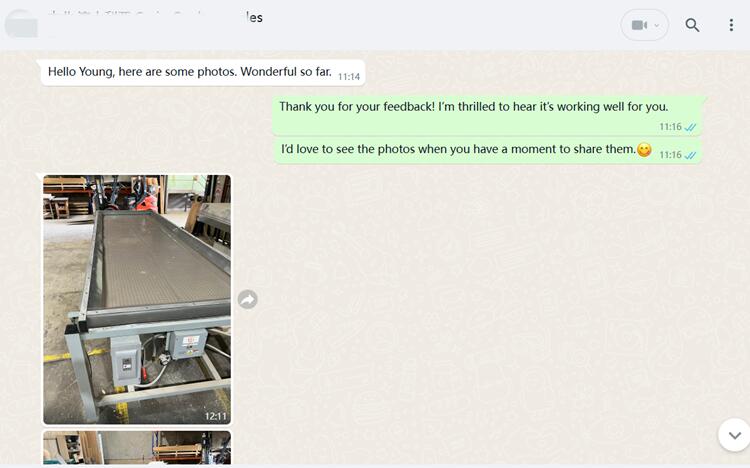
Top Silicone Membrane for Vacuum Forming, Pressing, Bending, and Laminating
At Deer Hunter, we specialize in manufacturing and supplying high-elasticity silicone rubber sheets, designed to deliver long service life and consistent results in your woodworking vacuum presses. Our specially formulated silicone sheets offer exceptional elongation and high tear strength, significantly extending their operational life in vacuum and lamination processes compared to natural rubber sheets.
The silicone membrane is available in a maximum width of 3800mm and can be cut to any roll length based on the customer’s specific requirements, subject to minimum order quantities. Thickness options range from 1mm to 3mm, ensuring that you get the ideal product for your application.
Quick Overview:
- High Tear Strength: Ideal for vacuum or lamination processes, with self-healing properties.
- High Flexibility: Elongates up to 860%, ensuring excellent adaptability in various applications.
- Excellent Abrasion Resistance: Withstands wear and tear even under heavy use.
- Puncture Resistance: Resists punctures without catastrophic failure.
- Durability & Lifespan: Built for long-term use in demanding environments.
- Tailored for Various Industries: Perfect for thermoforming solid surfaces, wood laminations, and even the aerospace and automotive industries.
- Color Options: Supplied as standard in gray transparent, with the ability to color match upon request.
- Tolerance: Rubber sheet tolerance allowance – width: 3%, length: 5%.
- Sold by Square Meter: Providing flexibility in purchasing based on project needs.
Technical Information:
Property | Value |
Color | Gray Transparent |
Material | 100% Silicone |
Roll Length (m) | Customizable |
Width (mm) | 3800mm Max |
Sold by Square Meter | Yes |
Hardness (Shore A) | 40-45 |
Maximum Working Temperature (°C) | 250 |
Minimum Working Temperature (°C) | -60 |
Tensile Strength (MPa) | 11.5 |
Elongation at Break (%) | 860 |
Note: Dimensions may vary; the values provided are typical. For example, a Canadian customer ordered 2pcs of 3mm X 3700mm X 5690mm for their glass lamination applications.
![]() | ![]() |
Woven bags packing | Wooden pallet |
Compatible Vacuum Press Brands for Our Silicone Membrane Sheets
The DH2211 silicone membrane offers excellent durability, high temperature resistance, and exceptional elongation properties, making it highly effective for forming intricate shapes. It is widely used in vacuum and thermoforming presses, wood lamination machines, and is also utilized in the composite industries, including parts for aerospace and automotive sectors.
When selecting a reliable supplier, trust is crucial. You’re in the right place to choose the ideal silicone sheet for your vacuum membrane presses. Our silicone rubber sheets are specifically designed to fit a variety of brands, including:
- SECABO
- ADAMIK
- BAO YUAN TONG
- BARTH
- BUGATOOL
- COLUMBUS
- ELKOM
- GLOBAL
- ISTRA-A
- ORMA
- RIBEX
- WISCHT
- Vac-U-Clamp
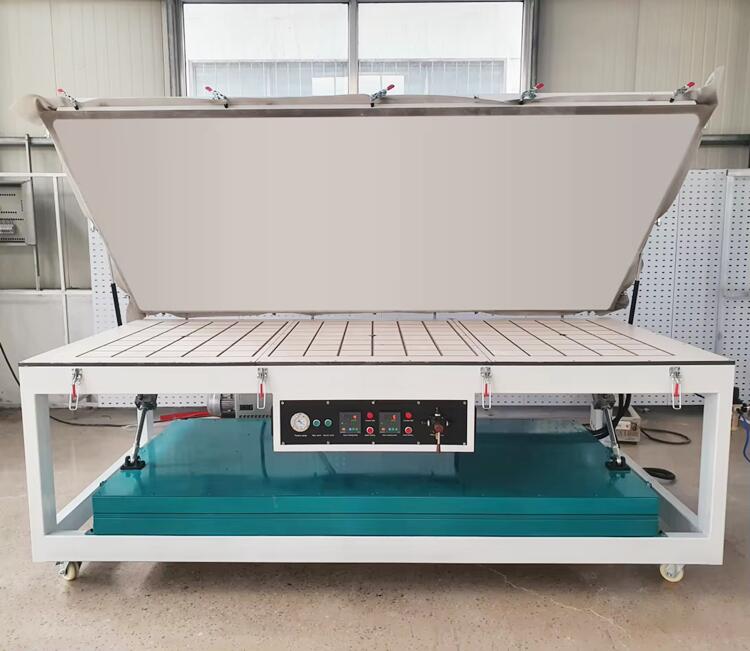
Whether you’re working with one of these brands or others, our silicone sheets ensure a perfect fit, offering unmatched performance in your vacuum press applications.
Step-by-Step Guide to Installing Silicone Sheets for Vacuum Presses
Proper installation of silicone sheets is crucial to ensure optimal performance and longevity. Follow these steps to install the silicone membrane correctly and avoid common issues during the vacuum press process.
1: Inspect the Silicone Membrane: Before installation, ensure that the silicone membrane is intact, smooth, and free from any defects.
2: Avoid Folding: When securing the silicone sheet onto the metal frame, make sure there are no folds in the membrane after installation.
3: Proper Tension: Do not stretch the silicone membrane too tightly. For new vacuum presses, ensure that the membrane is not folded during installation.
4: Surface Preparation: Typically, the frosted or smooth side of the membrane is the working surface. Apply talc powder to reduce surface friction and electrostatic effects. This will help prevent defects caused by uneven temperature distribution on the PVC foil. Talc powder can be reapplied after every 500 sqm of wood parts processed.
5: Cushion Placement: Position the cushions correctly, ensuring minimal gaps between each one. It is important to have a continuous cushion beneath the wooden working unit, especially at the sharp corners. The cushion plate can be indented by approximately 0.5cm at the sharp corners to ensure proper alignment.
6: Distance from the Metal Frame: For higher wooden parts, ensure they are placed at least 15cm away from the metal frame. Door panels should be placed 10cm away from the frame.
7: Avoid Re-Pressing Door Panels: Once the PVC films are cut, do not press door panels or parts again.
8: Stop the Machine if Issues Arise: If there is a loss of pump pressure, abnormal noise, or silicone sheet breakage, stop the vacuum press immediately. Once the air has been fully released, disassemble the silicone membrane and fix the issue before resuming operation.
9: Handle Repeated Breakage: If the silicone rubber sheet breaks in the same spot twice, investigate and resolve the issue before replacing the sheet.
Note: Deer Hunter reserves the final explanation for the above instructions.
Key Steps in the Vacuum Forming Process
This video showcases one of our customers using our 3mm thick high-quality silicone membrane, with 860% elasticity, in their multi-function vacuum membrane press to thermoform solid surface washing basins.
The vacuum forming process involves six essential steps that require precision and technical expertise. These steps should be performed with care to achieve the best results.
Step 1: Mold Preparation
The process begins with preparing the mold. The mold will be used to shape the final product and can be made from various materials, such as wood, MDF, or polystyrene. Ideally, the mold should have angled edges to facilitate the easy removal of the finished product.
Step 2: Placing the Mold on the Vacuum Former
Place the mold into the vacuum former, ensuring that the silicone sheet is held above the mold, without making contact with it.
Step 3: Heating the Material
Next, position the heater in the vacuum former above the material. The heater will warm the material to make it flexible and moldable.
Step 4: Positioning the Mold
Once the material is sufficiently heated and flexible, use a handle to lift the shelf holding the mold into position.
Step 5: Turning On the Vacuum Former
Turn on the vacuum former to remove air from the machine. This step creates the vacuum that pulls the heated material into the mold, allowing it to take on the shape of the mold.
Step 6: Removing the Formed Sheet
After the material has cooled and solidified, remove it from the vacuum former. The mold can then be taken out, and any excess or unwanted material is trimmed from the formed sheet.
How to Extend the Lifespan and Optimize the Use of Silicone Membranes
Silicone membranes are known for their durability, flexibility, and resistance to high temperatures, but their longevity and performance depend heavily on proper handling, storage, and maintenance. With the right care, high-quality silicone membranes can last well over five years, making them a reliable investment for vacuum pressing applications.
To help you get the most out of your silicone sheets, follow these best practices:
1. Store Properly to Prevent Degradation
(1) Keep silicone sheets in a cool, dry place, away from direct sunlight, as UV exposure can degrade elasticity over time.
(2) Store in clean environments free from oils, acids, and organic solvents that could weaken the material.
(3) Maintain a humidity level below 80% and store at room temperature for long-term preservation.
2. Handle with Care Upon Receipt
(1) Inspect the packaging immediately upon arrival for any visible damage. If defects are found, report them to the supplier promptly.
(2) Avoid unnecessary folding or stretching during handling and installation to maintain the membrane’s structural integrity.
3. Clean Regularly, but Gently
(1) Wash silicone membranes using mild detergent and warm water to remove dust and residue.
(2) Avoid harsh chemicals and solvents, as these can break down the material over time and shorten its lifespan.
4. Monitor for Wear and Tear
(1) Perform regular inspections to check for early signs of degradation, such as small tears or reduced elasticity.
(2) Identifying minor issues early can prevent major damage and reduce the frequency of replacements.
By following these simple yet effective maintenance steps, you can ensure your silicone membranes remain in peak condition, delivering consistent performance and long-term cost savings for your vacuum pressing operations.
Journey to Order Silicone Vacuum Membranes
We welcome end users, distributors, and wholesalers to order our tear-resistant silicone sheets. Below is the typical order process:
1. Send Request for Quotation (RFQ)
Contact us to request a quote based on your specific needs.
2. Analyze and Select Products
Review and select the appropriate silicone membrane products for your application.
3. Negotiate Contract and Submit Purchase Order (PO)
Finalize the terms and place the order by submitting a purchase order.
4. Receive and Review Invoice
Upon receipt of the invoice, carefully verify the details.
5. Authorize Invoice and Pay Advance
Approve the invoice and pay the required deposit.
6. Mass Production Begins
Once the advance is received, production of the silicone sheets begins.
7. Production Completion and Pay Balance
Upon completion of production, settle the remaining balance.
8. Packing and Shipping
The goods are carefully packed and shipped to your designated address.
9. Goods Receipt and Record Keeping
Upon receiving the goods, ensure everything is in order and maintain accurate records.
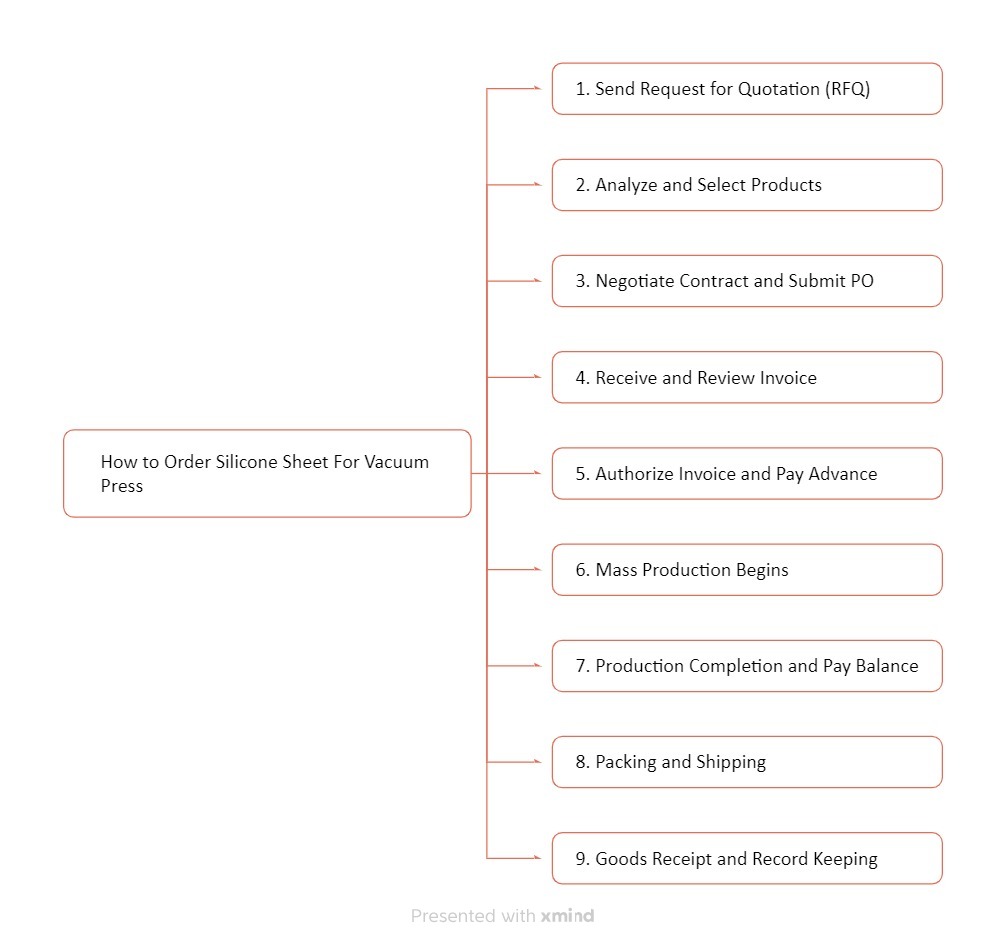
Note: If you have any concerns at any step of this journey, feel free to contact us.
The Most Common Question: Can a Damaged Silicone Membrane Be Repaired?
With frequent use, silicone membranes naturally age and may eventually suffer wear, tear, or accidental cuts. One of the most common questions we receive is:
“If the silicone membrane gets damaged or cut, can it be repaired? What adhesive should be used?”
Our answer depends on the severity of the damage:
(1) Small Cuts: Can be repaired using silicone glue to bond the edges back together.
(2) Larger Cuts: Require a silicone patch combined with silicone glue for extra reinforcement.
(3) Extensive Damage: If the cut is too large, it’s best to replace the membrane to maintain optimal performance.
For the best results, we recommend sourcing high-quality silicone glue from a reliable brand locally, such as Dow Corning (DOWSIL). This ensures a strong, durable repair and helps extend the lifespan of your membrane.
Final Thoughts: Let’s Talk Membranes!
Alright, now it’s your turn!
We hope this guide has shed some light on the wonderful world of silicone membranes and helped you get one step closer to finding the perfect fit for your vacuum forming machine.
Still have questions? Need help picking the right thickness, texture, or stretchiness for your application? Whether you’re laminating veneers, bending plywood, forming MDF thermofoil, or shaping solid surfaces, we’ve got you covered.
We are here to help! Drop an inquiry in the right contact form, or if you prefer good old-fashioned human interaction, call, text, or WhatsApp us at +86-13823789007, or shoot us an email at sales@cndeerhunter.com.
Let’s make sure your vacuum press is working like a pro, and your laminations are as smooth as they should be. 🚀