Selecting the right vacuum press membrane can feel like picking between coffee and tea—both do the job, but the best choice depends on your taste (or in this case, your vacuum pressing needs). Two of the most popular contenders in this space are silicone membranes and natural rubber membranes. They each have their strengths, but if you choose the wrong one, you might end up with wrinkles, weak adhesion, or a frustrating lamination process.
Silicone membranes boast high heat resistance, excellent elasticity, and durability, making them the go-to choice for thermoforming solid surfaces, laminating wood, and working with composites. On the other hand, natural rubber membranes are known for their tear strength, cost-effectiveness, and high flexibility, making them the favorite for veneering, laminating, and woodworking applications.
So, which one is a great fit for you? Should you go for heat-resistant and flexible silicone, or is tough, budget-friendly natural rubber the better option? In this guide, we’ll break down their key differences, pros and cons, and best applications, helping you make an informed choice. Plus, we will share some tips on where to find reliable suppliers so you can confidently place your next order.
By the end of this read, I’m sure that you will be equipped to choose the best vacuum press membrane for your specific needs—no more guessing, no more surprises, just smooth and efficient pressing every time.
What Are Silicone Membranes?
Silicone membranes are flexible, heat-resistant rubber sheets used in vacuum pressing, thermoforming, and composite molding. They withstand temperatures up to 250°C, making them ideal for high-precision shaping and laminating applications.
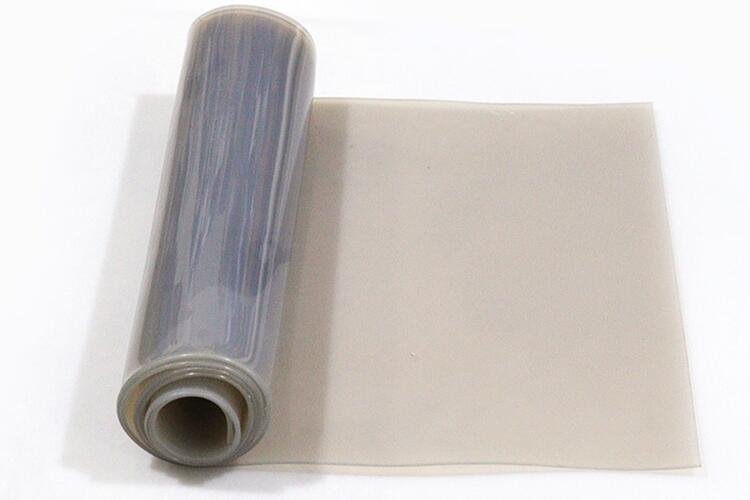
Key Features of Silicone Membranes:
✔ Superior heat resistance – Can withstand up to 250°C (482℉), making them perfect for high-temperature vacuum forming and laminating.
✔ Exceptional elasticity – Stretching up to 860%, allowing for detailed shaping and molding.
✔ Chemical resistance – Unaffected by most solvents, UV exposure, and environmental degradation.
✔ Long-lasting durability – Highly resistant to tearing, wear, and repeated use in extreme conditions.
✔ Versatile applications – Used in woodworking, composite manufacturing, sublimation printing, and automotive thermoforming.
Common Uses of Silicone Membranes:
✔ Thermoforming solid surfaces – Ideal for materials like Corian, Hi-Macs, Staron, and Kerrock.
✔ High-heat lamination – Suitable for hot press vacuum applications.
✔ Sublimation and printing – Ensuring even pressure for detailed image transfers.
✔ Laminating foil and veneer – Used in furniture, cabinetry, and decorative laminates.
What Are Natural Rubber Membranes?
Natural rubber membranes are strong, flexible, and cost-effective rubber sheets widely used in woodworking, veneering, and laminating applications. With exceptional tear strength and elasticity, they provide reliable performance in vacuum presses where high pressure is required.
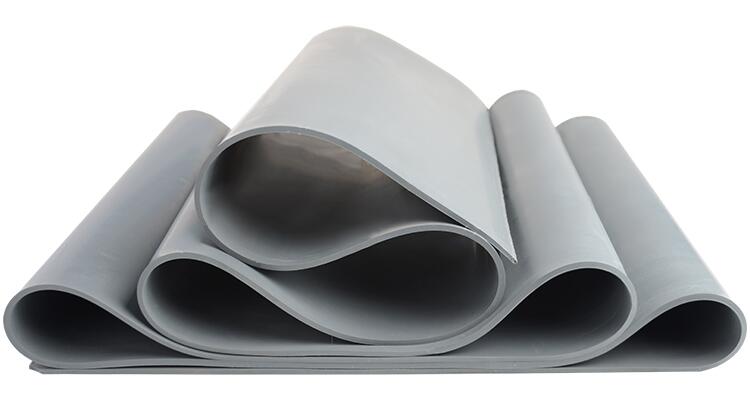
However, their temperature resistance is lower (up to 130°C), and when exposed to slightly higher temperatures or prolonged operation, they may release a noticeable odor.
Additionally, their lifespan is generally shorter compared to silicone membranes, especially in demanding applications.
Key Features of Natural Rubber Membranes:
✔ High tear strength – Offers superior durability for repetitive vacuum press cycles.
✔ Great flexibility – Provides 700% elongation, allowing it to adapt to different surface shapes.
✔ Cost-effective – More affordable compared to silicone membranes while still delivering reliable performance.
✔ Ideal for woodworking – Commonly used for laminating wood, veneer, leather, and PVC foil.
✔ Moderate heat resistance – Can handle temperatures up to 130°C (266℉), suitable for warm press applications.
Common Uses of Natural Rubber Membranes:
✔ Veneer and foil lamination – Used for furniture, cabinetry, and decorative wood applications.
✔ Molded wood production – Helps shape curved wooden surfaces with precision.
✔ Leather and textile pressing – Common in fashion and upholstery manufacturing.
✔ Cost-sensitive vacuum forming – Preferred for applications where extreme heat is not required.
As we continue, we’ll dive deeper into a side-by-side comparison to help you make the most informed decision for your specific vacuum pressing needs.
Silicone vs. Natural Rubber: Technical Specifications Breakdown
Recently, I received an inquiry from a customer in Turkey who specializes in the production and sales of woodworking machines. Many of their vacuum laminating machines, used for covering wooden materials with PVC, rely heavily on rubber membrane sheets.
For years, they had been sourcing these membranes from Europe, but due to rising costs, they decided to explore alternative materials from China. To ensure they could find a suitable replacement, the customer shared technical specifications in image form for the membranes they currently sell.
After reviewing and organizing their information, I compiled the following technical data he mentioned for both natural rubber and silicone membranes, making it easier to compare and evaluate potential alternatives.
Natural Rubber Membrane Specifications
Category | Natural Rubber Membrane |
Material | Natural Rubber |
Color | Grey |
Surface Texture | Smooth / Smooth, Smooth / Textured |
Thickness | 2mm, 2.5mm, 3mm, 4mm |
Weight | 4.3 ± 0.1 kg/m² |
Hardness | 42 ± 3 Shore A |
Maximum Production Width | 2000mm |
Temperature Resistance | -20°C to 130°C |
Antistatic | No |
Tensile Strength | 20 N/mm² ± 10% |
Elongation | 600% ± 10% |
Modulus 100% | 1 N/mm² ± 10% |
Tear Strength | 60 N ± 10% |
Resistance | Excellent resistance against diathermic oilsGood resetting ability and yield strength |
Application | High-pressure laminating |
Silicone Membrane Specifications
Category | Silicone Membrane |
Material | Silicone Rubber |
Color | Milky White |
Surface Texture | Smooth / Textured |
Thickness | 3.0mm ± 0.1mm |
Weight | 3.25 ± 0.1 kg/m² |
Hardness | 50 ± 3 Shore A |
Maximum Production Width | 2000mm |
Temperature Resistance | -50°C to 200°C |
Antistatic | No |
Tensile Strength | 9 N/mm² ± 10% |
Elongation | 700% ± 10% |
Modulus 100% | 1 N/mm² ± 10% |
Tear Strength | 90 N ± 10% |
Resistance | Very good ozone resistanceGood acid and lye resistanceLower resistance to solvents |
Application | High-pressure laminating at high temperatures |
Since China does not produce natural rubber membranes, I provided details of our exclusive DH2211 silicone membrane as the best potential alternative.
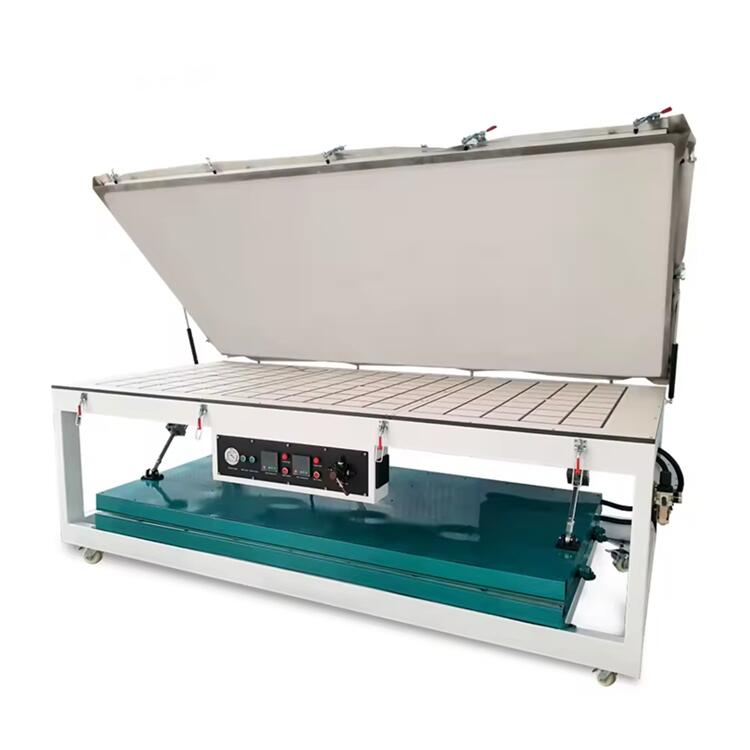
Silicone Membrane Specifications from Our Product DH2211
Category | Silicone Membrane (DH2211) |
Material | Silicone |
Color | Gray Transparent |
Surface Texture | Smooth / Smooth, Smooth / Textured |
Standard Thickness | 1mm, 2mm, 3mm |
Maximum Width | Up to 3800mm seamless |
Density | 1.25 ± 0.05 g/cm³ |
Hardness | 45 ± 5 Shore A |
Tensile Strength | 11.5 MPa |
Tear Strength | 45 N/mm |
Elongation | 860% |
Resilience | 25% |
Maximum Temperature Resistance | Up to 250°C |
Resistance Features | Excellent ozone resistanceGood acid and lye resistanceLower resistance to solvents |
Application | Used in thermoforming, composite vacuum pressing, and solid surface manufacturing |
You can also click and download the Technical Data Sheet of DH2211 here.
Understanding the Variability in Technical Specifications
The above specifications serve as reference values, but it’s important to note that each supplier may have slight variations based on:
- Raw material composition
- Manufacturing techniques
- Specific end-use applications
Key Takeaway: Choosing the Right Membrane
A higher specification does not necessarily mean better performance for every machine. Instead, compatibility with your vacuum press, application needs, and budget constraints should be the primary factors in selecting the ideal membrane.
My story with this Turkish customer is still unfolding, and the trial order has already been completed. If you’re interested in the follow-up, I’d be happy to share more details in a separate blog.
In the next section, we will explore the essential factors to consider when choosing between silicone and natural rubber membranes, helping you make a well-informed decision.
Key Considerations for the Right Vacuum Press Membrane
Whether you’re working with wood veneers, solid surfaces, or composites, a well-matched membrane ensures consistent performance, durability, and cost efficiency.
Here are the most important factors to evaluate:
1: Application Requirements: Matching the Membrane to Your Needs
Before looking at materials, start by identifying how the membrane will be used. Different applications require different properties:
- High-temperature thermoforming → Silicone membranes are best due to their 250°C heat resistance.
- Wood veneer and furniture laminating → Natural rubber membranes offer strong tear resistance and flexibility.
- Deep forming or curved surfaces → A thick, highly elastic membrane is ideal.
2: Compatibility with Adhesives & Processing Conditions
Not all membranes work well with all adhesives and press conditions.
- Silicone membranes resist most solvents, chemicals, and adhesives, making them ideal for high-heat vacuum pressing.
- Natural rubber membranes work well with wood veneers and PVC foils but may degrade when exposed to certain adhesives or excessive heat.
Check compatibility with your adhesives, temperatures, and vacuum press settings before making a choice.
3: Material Selection: Durability & Performance
The membrane material determines its resistance to heat, stretching, and wear.
- Silicone → Best for high-heat applications and materials requiring deep shaping.
- Natural Rubber → More cost-effective and suitable for woodworking and laminating applications.
- Polyurethane & PVC → Less common but used for specialized applications requiring moderate flexibility.
For demanding, high-temperature environments, silicone is the clear winner. For cost-sensitive applications, natural rubber is a strong contender.
4: Surface Texture – Why Both Smooth/Smooth and Smooth/Textured Exist
Silicone membranes are typically offered in two surface configurations: smooth/smooth and smooth/textured. So why both?
- Identification Made Easy: Some manufacturers only offer smooth surfaces on both sides, which can make it difficult to distinguish between brands or membrane types during use. By offering a smooth/textured option, it becomes easier to differentiate between the working surface and the backing layer.
- Application Flexibility: In most cases, customers use the smooth side as the working surface. However, the textured side can be beneficial when better airflow or breathability is required—such as in applications that involve curved parts or deep drawing.
- Manufacturing Advantage: From a production standpoint, the smooth/textured configuration helps reduce the risk of air entrapment between layers, resulting in fewer bubbles and a higher yield rate.
At Deer Hunter, both types are readily available. If you’re unsure which one suits your application best, our engineers strongly recommend testing a small sample first—we’ll ship it to you free of charge, including shipping.
5: Thickness: Strength vs. Flexibility
Membrane thickness affects durability and ability to conform to complex shapes.
- 1mm–2mm → Highly flexible, ideal for detailed shaping and deep forming.
- 2.5mm–3mm → Balanced durability and stretchability for general thermoforming and wood lamination.
- 4mm and above → More wear-resistant but less flexible, best for high-pressure applications.
6: Cost: Short-Term vs. Long-Term Value
Price varies based on material, thickness, and supplier, but focusing solely on cost can be misleading.
- Silicone membranes → Higher upfront cost but longer lifespan and better heat resistance.
- Natural rubber membranes → More affordable initially, but may require more frequent replacements.
Instead of just looking at price, consider long-term durability, replacement frequency, and overall cost-effectiveness.
7: Supplier & Product Quality
Reliable suppliers ensure consistent quality and optimal performance:
- Check for certifications and technical data that verify material quality.
- Request samples before placing bulk orders.
- Look for manufacturers offering custom sizing and expert support.
There is no universal best choice—your selection should depend on specific processing needs, material compatibility, and budget.
A well-matched membrane enhances lamination quality, operational efficiency, and overall durability.
Next, we’ll explore where to order high-quality silicone and natural rubber membranes and how to get the best deal.
Finding a Reliable Supplier for Vacuum Press Membranes
Selecting the right supplier for silicone and natural rubber membranes is just as important as choosing the right material. With many manufacturers in the market, it’s essential to work with a trusted provider to ensure consistent quality, performance, and long-term reliability.
Why Supplier Quality Matters
A reliable supplier ensures that the membrane:
- Meets industry standards for durability, elasticity, and temperature resistance
- Provides consistent performance across different production cycles
- Offers customization options for specific press requirements
- Delivers on time with strong after-sales support
Where to Source Silicone Membranes
Silicone membranes, known for their high heat resistance and flexibility, are used in thermoforming, laminating, and composite manufacturing.
✔ Deer Hunter – A leading supplier of premium silicone membranes for vacuum presses, offering high-temperature resistance, excellent elasticity, and durable material stability. Their membranes are widely used in woodworking, thermoforming, and composite industries, providing reliable performance across multiple applications.
Next, we’ll explore the best ordering practices to ensure you get the right membrane for your vacuum press needs.
Steps to Ordering Vacuum Press Membranes
Ordering vacuum forming membranes is more than just clicking “buy now.” To ensure you receive a high-quality product that meets your requirements, it’s essential to follow a structured approach. A reliable supplier, accurate specifications, and proper logistics planning will help prevent delays, mismatched materials, or unexpected costs.
Follow these steps for a smooth purchasing process:
1: Define Your Requirements
Before placing an order, identify the exact type, size, and thickness of the membrane based on your vacuum press application. Key factors to determine include:
- Material type (silicone for high heat applications)
- Thickness (1mm–3mm for flexibility, 4mm+ for durability)
- Surface texture (smooth for even sealing, textured for better grip)
- Size (ensure it matches your press dimensions)
2: Research and Compare Suppliers
Finding a reputable supplier is crucial for consistent quality and reliable delivery. Research potential manufacturers through:
- Company websites and product catalogs
- Online marketplaces (Google, B2B platforms)
- Industry reviews and customer testimonials
- Compare pricing, specifications, and supplier credibility before making a decision.
3: Request Quotes & Negotiate Terms
Contact multiple suppliers and request detailed quotations based on your required specifications. When reviewing quotes, pay attention to:
- Unit price (bulk orders may offer better pricing)
- Minimum order quantity (MOQ)
- Shipping costs and lead time
- Payment terms (deposit, balance on delivery, etc.)
Negotiating favorable terms, especially for bulk purchases, can result in better pricing and after-sales support.
4: Place Your Order & Confirm Logistics
Once a supplier is selected, finalize the order by providing:
- Exact membrane specifications
- Shipping details (address, preferred carrier, delivery timeline)
- Payment confirmation based on agreed terms
Ensure all details are documented to avoid misunderstandings.
5: Track and Inspect Your Shipment
After shipping, monitor the order status to ensure timely delivery. Upon receipt, inspect the membranes for:
- Surface defects or damage during transit
- Correct dimensions and specifications
- Any unexpected inconsistencies
If issues arise, contact the supplier immediately to resolve them.
6: Store & Maintain the Membranes Properly
To prolong the lifespan of your silicone membrane:
- Store it in a cool, dry place away from direct sunlight
- Avoid contact with sharp objects that may cause damage
- Keep it free from dust or debris to maintain its sealing efficiency
7: Provide Feedback & Maintain Supplier Relations
Building a long-term relationship with a trusted supplier ensures consistent quality, future order flexibility, and better pricing. Regular communication and feedback help both parties improve product offerings and service reliability.
Ordering a vacuum press membrane isn’t just about finding the right material—it’s about choosing a reliable supplier, confirming specifications, and ensuring smooth delivery. Following these structured steps helps you get the best quality membrane at the right price with minimal hassle.
In the next section, we’ll wrap things up with some final recommendations on selecting the best vacuum press membrane for your needs.
Final Decision: Which Membrane Wins?
So, after all this talk about silicone vs. natural rubber membranes, where do we land? Well, if you were hoping for a one-size-fits-all answer, I hate to break it to you—there isn’t one. But don’t worry, you’re not alone in this!
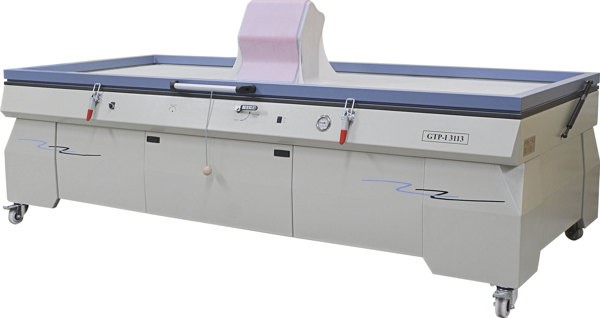
Let’s recap:
- Natural rubber membranes are affordable, elastic, and great for woodworking. But throw too much heat at them, and they’ll tap out early.
- Silicone membranes are heat-resistant, durable, and perfect for high-temperature applications, but they might require a little extra room in your budget.
Disclaimer:
Deer Hunter supplies only silicone membranes. Equipment or accessories shown are for illustration purposes only.
So, what’s the best choice? It all depends on your vacuum press, materials, and production needs. If your project involves thermoforming solid surfaces at high temperatures, silicone is your best bet. If you’re veneering furniture and cost matters most, natural rubber will do the job just fine.
At the end of the day, the best membrane is the one that works for YOU.
Now, your turn!
Are you all set to grab the perfect vacuum press membrane, or are you still stuck in the decision-making loop?
Maybe you have a question about compatibility, thickness, or why silicone costs more than your morning coffee habit.
Either way, I’d love to help. Drop an inquiry in the form on the right table, or you can contact us at email export@cndeerhunter.com or call us +86-13823789007 directly. And let’s find the best membrane for your needs.
And remember—when in doubt, don’t let your vacuum press do the guessing. Let’s make sure it’s pressing like a pro!