Ever stared at a list of silicone rubber sheets, feeling like you were deciphering an ancient scroll?
You’re not alone!
Picking the right silicone rubber sheet for your vacuum membrane press can feel overwhelming. Too thick, and you might lose flexibility; too thin, and durability takes a hit. The wrong choice could mean higher costs, weak performance, or a frustrating purchasing experience that wastes your time.
But here’s the good news. You don’t need a college degree in material science to get it right. Stick with us, and you’ll soon discover a high-temperature silicone rubber sheet that stands out in vacuum pressing for its impressive heat resistance, resilience, and longevity. Whether you’re working on veneering, laminating, bending wood, 3D foil / film and thermoforming, having the right membrane makes all the difference.
In today’s article, we’ll break down everything you need to know about silicone rubber sheets—their key features, benefits, and how to select the perfect one for your vacuum pressing applications.
Let’s dive in and make sure your vacuum forming process is running like a dream.
Vacuum Membrane Press 101: The Magic Behind the Suction!
A “vacuum membrane press” is a machine that uses a flexible membrane, placed under a vacuum, to apply even pressure onto a workpiece, allowing for precise shaping, laminating, and bending of materials like wood veneer, plastic, or composite materials, often used in woodworking and thermoforming applications where complex curved surfaces are required; essentially, the vacuum pulls the membrane tightly against the material, conforming it to the desired shape.
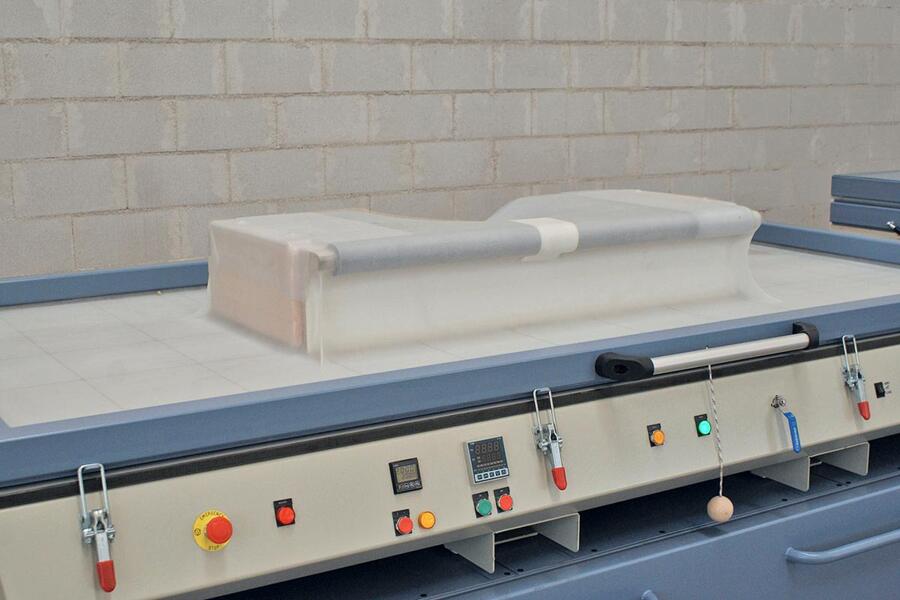
Common Applications
Vacuum membrane presses are widely used in woodworking, furniture manufacturing, and thermoforming due to their ability to apply even pressure across a surface. Some of the most common applications include:
✔ Veneering – Bonding thin wood veneers onto MDF, plywood, or other substrates.
✔ Laminating – Creating multi-layered surfaces by bonding different materials together.
✔ Bending Wood – Shaping curved or intricate wood designs that would be difficult to achieve with traditional clamps.
✔ Thermoforming Plastics – Molding acrylic, PVC, and other plastic sheets into detailed shapes.
Key Benefits of a Vacuum Membrane Press
✔ Even Pressure Distribution – Ensures uniform adhesion and shaping.
✔ Precision & Complexity – Capable of handling intricate curves and deep molds.
✔ Material Versatility – Works with wood, plastics, composites, and more.
✔ Efficient & Cost-Effective – Reduces labor-intensive clamping and improves production efficiency.
Whether you’re in woodworking, cabinetry, or composite manufacturing, a vacuum membrane press is an indispensable tool for achieving high-quality, detailed, and durable results.
Meet Your Press’s Best Friend: The Mighty Silicone Rubber Sheet
In a vacuum membrane press, the flexible membrane is essential for shaping, laminating, and molding various materials. To handle this demanding task, the membrane must be highly elastic, heat-resistant, and durable—qualities that make silicone rubber sheets the top choice for vacuum forming applications.
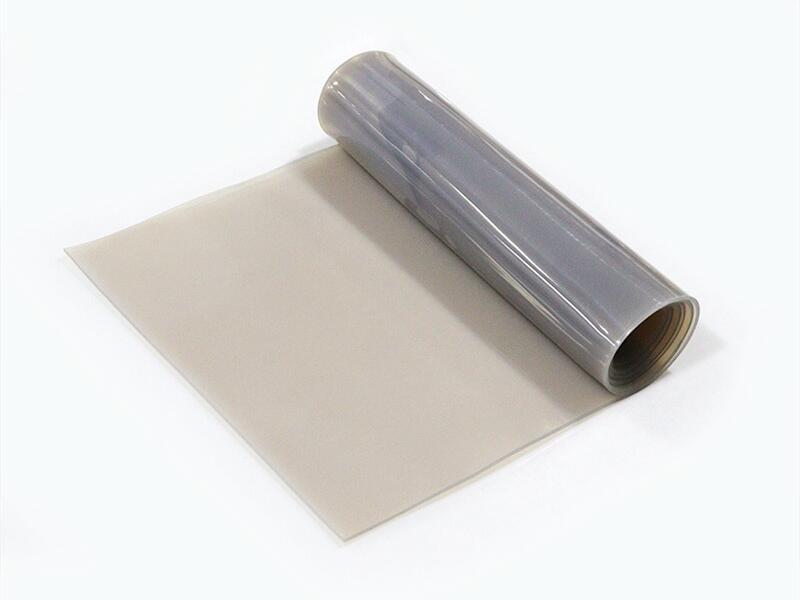
A vacuum pressing silicone rubber sheet is a thin yet highly resilient material designed to endure extreme temperatures, repeated stretching, and continuous use. When placed over a workpiece, the silicone sheet stretches, conforms, and applies even pressure, ensuring smooth, seamless fit without air pockets or inconsistencies.
Why Is Silicone Rubber the Preferred Choice?
✔ High-Temperature Resistance – Withstands heat up to 250°C, making it ideal for thermoforming and laminating applications.
✔ Exceptional Flexibility – Stretches without losing shape, ensuring precision in molding complex surfaces.
✔ Long-Lasting Durability – Resistant to wear, tearing, and degradation, even under repeated use.
✔ Versatile Applications – Used in woodworking, composite manufacturing, and solid surface forming.
Whether you’re veneering furniture, forming thermoplastic sheets, or laminating curved surfaces, a high-quality silicone rubber sheet ensures consistent results, enhanced efficiency, and a flawless finish in every vacuum pressing operation.
Why Silicone Rubber Sheets Are Hotter Than a Summer Sidewalk
Silicone rubber sheets have become an essential component in vacuum membrane presses, offering unmatched performance across various industries. Their unique properties make them the go-to choice for thermoforming, laminating, veneering, and composite molding. But what exactly makes these sheets so sought after? Let’s take a closer look!
1) Exceptional Durability & Elasticity
A silicone membrane sheet is built to withstand extreme stretching and repeated use without losing its shape. Thanks to its high wear resistance, a silicone rubber membrane can endure heavy-duty vacuum pressing without tearing or degrading, making it ideal for long-term industrial applications.
2) Customizable Colors & Surface Finishes
Silicone sheets are available in various colors to meet different manufacturing needs. While color does not affect performance, it is often used to distinguish different suppliers or grades. Additionally, smooth and textured surfaces allow for greater versatility, ensuring the perfect fit for different vacuum press applications.
3) Multiple Grades for Different Applications
From thin-gauge silicone sheets for thermoforming solid surfaces to thicker, high-strength silicone membrane sheets for high-pressure vacuum forming, the variety of options ensures optimal performance for different industries. Consulting an experienced supplier ensures you get the right silicone rubber membrane for your specific needs.
4) Cost-Effective & Long-Lasting Solution
Despite their advanced properties, silicone sheets offer an excellent balance of performance and affordability. Compared to natural rubber alternatives, silicone membrane sheets provide greater heat resistance, durability, and flexibility, making them a smart investment for any vacuum pressing operation.
With superior elasticity, heat tolerance up to 250°C, and excellent resilience, silicone rubber sheets remain the top choice for manufacturers looking to achieve precision, efficiency, and long-lasting performance in their vacuum press applications.
The Must-Know Checklist for Choosing the Right Silicone Sheet
Silicone rubber sheets are widely used in vacuum membrane presses due to their exceptional durability, heat resistance, and flexibility. Whether you’re working with thermoforming, veneering, or composite molding, selecting the right silicone sheet is crucial for achieving optimal performance. Below are the top considerations to keep in mind when choosing a silicone membrane sheet for your vacuum press.
1) Heat Resistance: Withstanding Extreme Temperatures
One of the standout features of silicone rubber sheets is their ability to endure high temperatures without degrading. Unlike other rubber materials, silicone membranes maintain their elasticity and structure even at working temperatures up to 250°C, making them ideal for vacuum pressing applications that involve heat-sensitive materials.
2) Superior Weathering Resistance
Unlike conventional rubbers, which deteriorate when exposed to UV rays and ozone, silicone sheets remain stable under extreme weather conditions. Their long-lasting resistance to environmental factors makes them perfect for applications requiring prolonged outdoor exposure or continuous thermal cycling.
3) Cold Resistance: Flexible Even in Sub-Zero Conditions
A high-quality silicone membrane sheet can withstand temperatures as low as -60°C to -70°C without becoming brittle. This cold-resistant property makes silicone rubber membranes suitable for industrial applications that require elasticity across a broad temperature range.
4) High Thermal Conductivity
Silicone sheets have excellent heat transfer properties, which help distribute temperature evenly during vacuum forming or laminating processes. This makes them an excellent choice for applications such as heat sinks, heating rollers, and high-precision molding, where uniform thermal conduction is essential.
5) Electrical Insulation Properties
With outstanding dielectric strength, silicone membrane sheets function as excellent electrical insulators. Unlike other rubber materials, they retain their insulating properties even when submerged in water or exposed to high voltages, making them ideal for applications that require superior electrical resistance.
6) Resistance to Steam and Moisture
Long-term exposure to moisture has little impact on silicone rubber sheets. They exhibit low water absorption and maintain their structural integrity even when exposed to high-pressure steam above 150°C. This makes silicone membranes a preferred choice in applications where resistance to steam is critical.
7) Resistance to Oils, Solvents, and Chemicals
Unlike organic rubbers, silicone membrane sheets offer excellent resistance to oils, solvents, and chemicals, especially at elevated temperatures above 100°C. This makes them suitable for use in environments where exposure to aggressive substances is common.
8) High Tensile and Tear Strength
One of the defining characteristics of silicone rubber membranes is their impressive tensile strength (11.5 MPa) and tear resistance. These properties allow them to withstand repeated use in demanding vacuum forming and laminating applications without compromising their structural integrity.
9) Fire Resistance: Slow Burning & Self-Extinguishing Options
Although silicone sheets do not catch fire easily, they tend to burn continuously once ignited. However, flame-retardant silicone rubber sheets can be manufactured by incorporating specialized additives, making them compliant with fire safety regulations for certain industrial applications.
Choosing the right silicone membrane sheet depends on your specific vacuum pressing requirements, whether it’s heat resistance, flexibility, or chemical stability. Understanding these factors will help ensure long-term performance and efficiency in your applications.
Shopping for Silicone Sheets? Don’t Let Confusion Cost You!
Selecting the right silicone rubber sheet for your vacuum membrane press requires careful evaluation of key factors to ensure compatibility with your specific application. From size and thickness to temperature resistance and surface finish, each detail plays a crucial role in achieving optimal performance. Below are the key considerations to keep in mind before making a purchase.
1) Size: Ensuring Proper Fit
Before purchasing a silicone sheet, it’s essential to determine the correct dimensions to fully cover the vacuum press table. Measuring the surface area and thickness of your workpiece ensures a seamless fit, preventing material shortages or installation difficulties.
2) Thickness: Balancing Durability & Flexibility
Thickness impacts both the lifespan and flexibility of a silicone membrane sheet.
✔ Thinner sheets (1mm-2mm) – Ideal for detailed shaping and complex molding.
✔ Standard thickness (2.5mm-3mm) – Balanced durability and elasticity for general vacuum pressing.
✔ Thicker sheets (4mm and above) – Best for high-pressure applications requiring long-term wear resistance.
3) Temperature Resistance: Matching Operating Conditions
Not all silicone rubber membranes are created equal when it comes to heat resistance. If your process involves high-temperature vacuum forming or thermoforming, ensure that the silicone membrane sheet can withstand working temperatures up to 250°C without degradation.
4) Abrasion Resistance: Maximizing Longevity
Different silicone sheets have varying levels of abrasion resistance. High-abrasion-resistant membranes are ideal for heavy-duty applications where repeated pressure and friction occur. If your vacuum press operates under frequent cycles, investing in a durable silicone rubber sheet will reduce wear and extend its lifespan.
5) Hardness (Shore Durometer): Finding the Right Elasticity
Silicone membrane sheets are available in various hardness levels, measured in Shore A durometer.
✔ Soft silicone sheets (40-50 Shore A) – Provide excellent flexibility for deep-draw forming and delicate shaping.
✔ Medium hardness (50-60 Shore A) – Suitable for general vacuum pressing and wood laminating.
✔ Harder sheets (60+ Shore A) – Offer superior tear resistance but may limit flexibility in complex shapes.
6) Surface Finish — Smooth/Smooth vs. Smooth/Textured
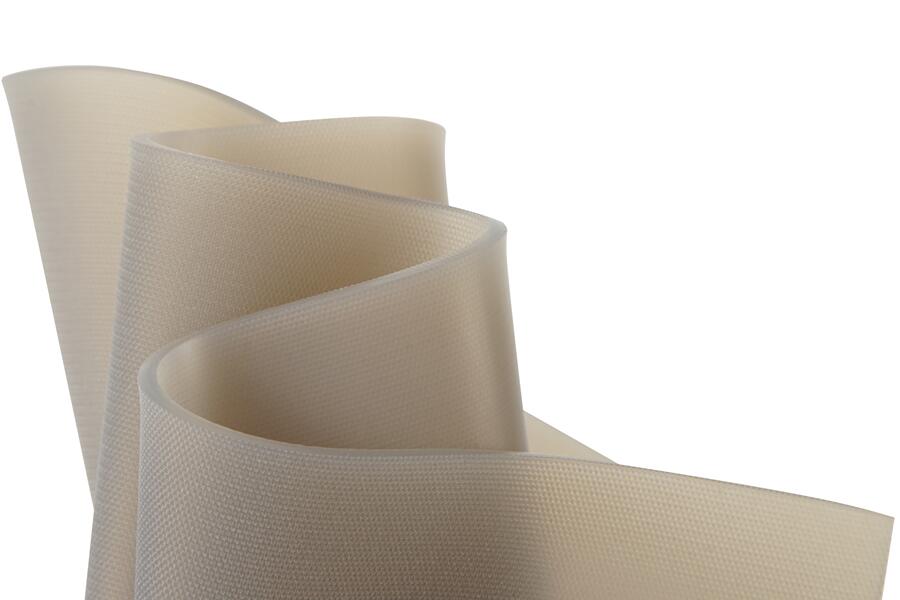
Why do we offer both?:
✔ Easy Identification – Smooth/textured membranes help distinguish between the working side and the backing, unlike dual-smooth types which can be hard to tell apart.
✔ Flexible Use – Most users work with the smooth side. The textured side, however, improves airflow—useful for deep forming or curved applications.
✔ Better Yield in Manufacturing – Smooth/textured membranes reduce air entrapment, minimizing bubbles and increasing production success rates.
Both options are available at Deer Hunter. Not sure which fits your application? Request a free sample—shipping included.
7) Cost vs. Long-Term Value
Price matters, but focusing only on the lowest cost can be misleading. High-quality silicone rubber sheets may come with a higher upfront price, but their longer lifespan, better heat resistance, and reduced replacement frequency provide greater value in the long run.
By carefully assessing these factors, you can select a silicone sheet that meets your vacuum press requirements while ensuring efficiency, durability, and cost-effectiveness.
Using a Silicone Sheet in Your Vacuum Press (Without Breaking a Sweat)
Installing and using a silicone rubber sheet correctly in a vacuum membrane press is essential for ensuring smooth operation, preventing premature wear, and achieving high-quality results. Below are the key steps to follow for proper usage.
Step 1: Inspect the Silicone Sheet
Before installation, carefully examine the silicone membrane sheet for any damage, cuts, or surface imperfections. A defective sheet can lead to air leaks, uneven pressing, or premature failure.
✔ Ensure the sheet is free from tears or weak spots.
✔ Avoid folding or overstretching when attaching it to the press frame.
✔ Do not install the sheet too tightly, as it may cause premature wear.
Step 2: Prepare the Working Surface
To improve performance and extend the lifespan of your silicone sheet, apply a thin layer of talc powder on the surface that will be in contact with the workpiece.
✔ Reduces surface friction and static buildup.
✔ Helps prevent materials from sticking to the membrane.
✔ Ensures uniform pressure distribution across the workpiece.
Step 3: Position Components Correctly
For optimal pressing, materials should be placed strategically inside the vacuum press:
✔ Keep wooden components at least 15 cm away from the metal frame.
✔ Door panels should be positioned at least 10 cm away from the press edges.
✔ Avoid re-pressing door panels and parts once the PVC film has been cut, as it may affect adhesion.
Step 4: Maintain Proper Vacuum Pressure
A well-regulated vacuum ensures effective lamination and forming.
✔ Monitor vacuum pressure levels to prevent air leakage.
✔ If you notice unusual noises or pressure drops, stop the machine immediately.
✔ Check seals and connections to prevent vacuum loss.
Step 5: Complete the Pressing Cycle and Inspect the Results
Once the vacuum pressing process is complete, carefully remove the workpiece.
✔ Allow the press to fully release air before disassembling.
✔ Inspect the pressed material for defects such as wrinkles or poor adhesion.
✔ If issues arise, adjust placement, pressure, or sheet positioning before the next cycle.
By following these steps, you can maximize the performance and longevity of your silicone rubber sheet, ensuring consistent, high-quality results in your vacuum membrane press operations.
Storage & Handling: Keep Your Silicone Sheets Happy and Healthy
Proper handling and storage of silicone rubber sheets are essential to maintaining their performance, flexibility, and longevity. Neglecting these precautions can lead to premature wear, reduced elasticity, or contamination that affects vacuum pressing results. Here are some key tips to ensure your silicone membrane sheets remain in top condition.
1) Avoid Contact with Oils and Harsh Chemicals
✔ Keep silicone sheets away from oils, acids, alkalis, and organic solvents, as these substances can degrade the material and reduce its effectiveness.
✔ Always clean hands and work surfaces before handling the sheets to prevent accidental contamination.
2) Protect from Direct Sunlight and Extreme Heat
✔ Prolonged exposure to UV light and excessive heat can weaken the silicone’s structure, leading to discoloration and reduced elasticity.
✔ Store sheets in a cool, dry place away from direct sunlight to preserve their integrity.
3) Inspect Packaging Before Use
✔ Always check the packaging upon delivery to ensure there are no signs of damage, moisture exposure, or contamination.
✔ If you notice defects or improper sealing, contact your supplier for replacements before use.
4) Store and Pack Sheets Properly
✔ When storing, roll up or fold sheets correctly to prevent unnecessary creasing or stretching.
✔ Use sturdy carton boxes or protective covers to shield them from dust, dirt, and environmental factors that may affect their surface.
By following these handling and storage best practices, you can extend the lifespan of your silicone rubber sheets and ensure they deliver consistent, high-quality results in your vacuum pressing applications.
Beyond the Press: Where Else Can Silicone Sheets Work Their Magic?
Over the past decade, Deer Hunter has continuously refined its silicone rubber sheets to meet the evolving needs of industries requiring precision vacuum pressing. These membranes offer outstanding heat resistance, flexibility, and durability, making them a preferred choice in multiple applications.
1) Vacuum Membrane Presses
✔ Silicone rubber sheets are widely used in furniture and woodworking, as well as in aviation, automotive, composite manufacturing, rigid foil lamination, plastic processing, and sublimation industries.
✔ In vacuum forming, high tear-strength silicone membranes ensure precise molding, even for intricate designs.
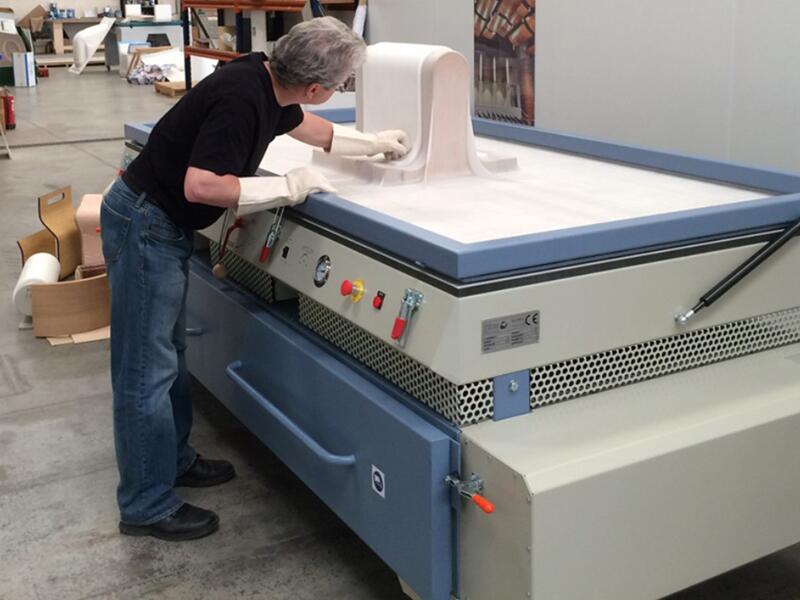
2) PVC Foil Lamination
✔ Used in furniture doors, kitchen cabinets, wall panels, and plywood, silicone membrane sheets provide consistent pressure distribution for high-quality thermoforming of solid surfaces and thermoplastic materials.
3) Wood Veneering & Cabinet Manufacturing
✔ Silicone and natural rubber membranes support seamless application of wood veneers and thermofoil door panels.
✔ Trusted by cabinet manufacturers and veneering specialists due to their elasticity and ability to handle intricate detailing.
4) Glass Lamination
✔ High-elasticity silicone sheets (up to 860% elongation) are commonly used as the core material for silicone vacuum bags in laminated glass production.
✔ These membranes provide the durability and flexibility needed to achieve flawless glass lamination.
5) Solar Panel Lamination
✔ Some manufacturers choose 3mm silicone rubber sheets for solar panel lamination, leveraging their high-temperature resistance.
✔ However, for solar lamination, we recommend alternative materials better suited to extreme heat and pressure conditions.
From furniture manufacturing to composite forming, silicone rubber sheets continue to prove their versatility and reliability in vacuum pressing applications.
Your Burning Questions About Silicone Rubber Sheets—Answered!
Here are some common questions manufacturers ask when considering silicone rubber sheets for vacuum membrane presses.
1) How Long Does a Silicone sheet Last?
Lifespan depends on working conditions, temperature, and operator handling. Under proper use, our high tear strength silicone sheets can last over 1-2 years in vacuum pressing.
2) Can a Damaged Silicone Rubber Sheet Be Repaired?
It depends on the severity of the damage:
Small cuts – Can be fixed using silicone adhesive.
Larger tears – Require a silicone patch with adhesive for reinforcement.
Severe damage – Replacement is recommended to maintain vacuum integrity.
For best results, we suggest using high-quality silicone glue, such as Dow Corning (DOWSIL).
3) What Packaging Options Are Available for Silicone Rubber Sheets?
To ensure safe transport, we provide:
Carton box – For single sheets, folded if necessary.
Wooden pallet/crate – Best for bulk shipments, preventing damage during transit.
4) What Can Damage Silicone Rubber Sheets?
While silicone rubber is highly resistant to environmental factors, it can be compromised by:
✔ Strong acids (e.g., concentrated sulfuric acid, hydrofluoric acid)
✔ Prolonged exposure to high-pressure steam
✔ Sharp objects or excessive stretching beyond its tear strength
5) Is Silicone Rubber Durable?
Absolutely! Silicone rubber sheets are known for their long lifespan, elasticity, and resistance to heat, chemicals, and wear. These qualities make them one of the most durable materials for vacuum membrane presses.
Still have questions? Reach out to us, and we’ll help you find the perfect silicone rubber sheet for your application!
Ready to Press Like a Pro? Let’s Get You the Perfect Silicone Sheet!
Well, there you have it—everything you need to know about silicone rubber sheets for vacuum presses.
By now, you’re probably either:
A) Ready to place an order and take your vacuum pressing game to the next level.
B) Still staring at your screen, wondering which silicone sheet is the one.
Either way, we’ve got you covered! Whether you need high-temperature resistance, maximum flexibility, or a custom solution, we’re here to help.
Let’s make your vacuum pressing smoother, more efficient, and stress-free.
Drop us a message, call us at +86-13823789007, or email sales@cndeerhunter.com.
We’ll get back to you faster than your vacuum press cycle!