As the global demand for clean and sustainable energy continues to rise, the quest for more efficient solar panels has become of utmost importance. In recent years, researchers and engineers have been relentlessly exploring cutting-edge techniques to enhance solar panel performance. Among these innovations, one solution stands out – silicone diaphragms in PV module lamination. This revolutionary technology has the potential to reshape the solar industry by vastly improving solar panel efficiency and durability.
In this informative article, we will delve deep into the transformative power of silicone diaphragms and their ability to optimize the lamination process, resulting in solar panels that generate higher electricity output and boast an extended operational lifespan.
Get ready to unveil the fascinating potential of this seemingly simple yet incredibly impactful photovoltaic diaphragms, as it paves the way for a brighter future in solar energy. So, without further ado, let us embark on a journey to explore the remarkable capabilities of silicone diaphragms in revolutionizing solar panel efficiency.
What Is Solar Panel Lamination?
Broadly speaking, Solar Panels = Solar PV Modules
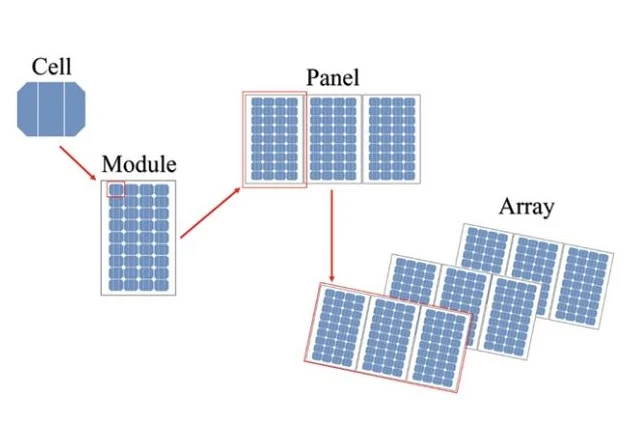
While this might be apparent to many readers engaged in the production of P.V. modules, our goal is to help everyone understand the rigorous demands and standards of this industry. Solar panels must endure outdoor exposure under all climatic conditions for 25 years or more, efficiently converting sunlight into electricity throughout their operational lifespan.
The lamination process plays a vital role in enhancing the panels’ durability and their ability to endure outdoor conditions. It involves encapsulating solar cells between several substrate layers, forming a “lay-up” that has been successfully used for over two decades.
A prevalent module lay-up includes tempered glass as the transparent top layer, followed by a layer of encapsulant, interconnected solar cells, another layer of encapsulant, and a UV stable film as the back sheet. This robust lay-up guarantees the modules’ optimal functioning and longevity.
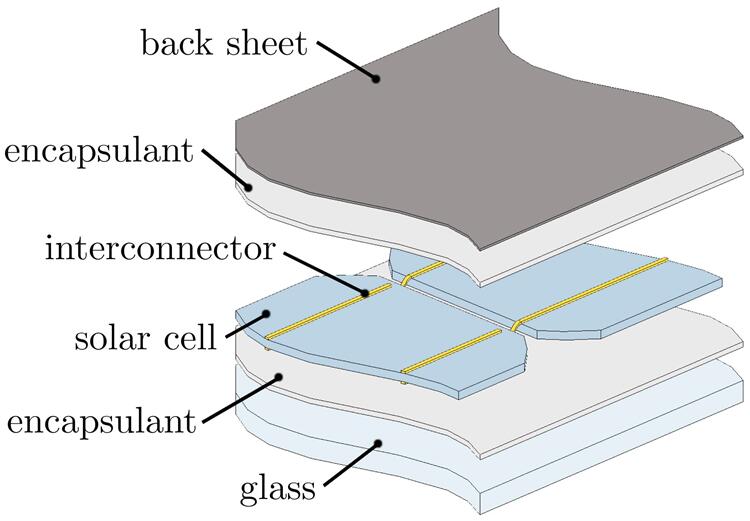
The encapsulant used in the lamination process is typically composed of Ethylene Vinyl Acetate (EVA). Over time, significant advancements have been made in this bonding material to address the issue of aggressive outgassing that occurs as a bi-product of the continuous lamination process.
Basic 6 Steps For Lamination Process
The solar panel lamination process is a procedure that involves the bonding of multiple layers of materials to form a complete solar panel. The process typically includes several steps, such as:
1. Preparation stage
Initial preparations involve arranging the materials for the lamination procedure, including solar cells, backing material, and encapsulant. Solar cells are often positioned within a jig to secure their placement throughout lamination.
2. Cleaning step
Both solar cells and backing material undergo thorough cleaning to eliminate any particles or impurities that could disrupt the bonding process.
3. Adhesive application
An adhesive substance is applied to the backing material to establish a bond between the solar cells and the substrate.
4. Encapsulation layer
A layer of encapsulant is carefully applied over the solar cells, serving to shield them and enhance the panel’s overall resilience.
5. Lamination process
The panel enters a solar laminator, where a combination of heat and pressure is employed to unite the layers. Following this, the panel is subjected to cooling, finalizing the lamination.
6. Performance evaluation
The completed panel undergoes rigorous testing to verify its compliance with prescribed performance standards.
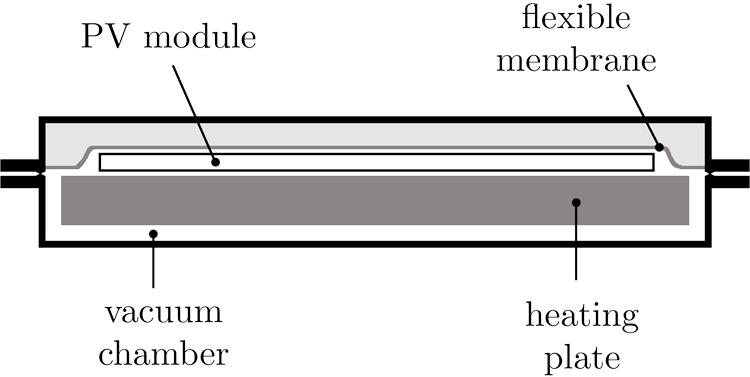
A solar module laminator is composed of a spacious heated platen housed within a vacuum chamber. This laminator usually functions at temperatures around 150°C (302°F). Loading and unloading of modules are made easy through the top opening of the laminator. The adaptable flexible membrane is put onto the top of the vacuum chamber either by clamping or bolting methods.
A Brief Introduction Of Solar Silicone Diaphragms
Solar silicone diaphragms are flexible membranes made from specialized silicone polymers for use in creating photovoltaic panels. They have excellent properties such as flexibility, insulation, and resistance to corrosion and heat, which help them withstand high pressure and temperature conditions during the process of making solar panels. They are designed specifically to meet the needs of many solar panel manufacturers, making them an important part of solar panel production.
Solar diaphragms should possess the following qualities:
(1) Adequate flexibility to precisely conform to the lay-up’s contours
(2) Sufficient strength to withstand repeated stretching under vacuum conditions
(3) Capability to resist high temperatures (typically around 150°C)
(4) Favorable properties for smooth production processes
(5) Endurance against the effects of EVA (ethylene vinyl acetate)
(6) Cost-effectiveness as an essential consumable
Top 7 Challenges Associated with Flexible Diaphragms
The common perception is that when a diaphragm fails before its expected lifespan, the blame is often placed on the diaphragm itself. However, from experiences and numerous technical visits conducted worldwide, it has become clear that various uncontrollable factors frequently play a significant role in diaphragm failures.
Deer Hunter has thoroughly examined these concerns and identified some of the most common issues. By avoiding these pitfalls, customers can significantly enhance the performance of their silicone flexible membranes.
Now, let’s examine these problems in greater detail:
1. Glass breakage during lamination can not only puncture the PTFE (Teflon) sheet, but also cause significant damage to the diaphragm with severe consequences.
2. EVA outgassing leads to chemical reactions and harmful impacts, making it a major challenge for diaphragms.
3. Excessive EVA deposits on the protective PTFE sheets can seep into diaphragms, causing cracks at critical stress points and resulting in premature failure.
4. Exposed open areas during lamination occur when the PTFE sheet lacks support on the laminator platen. As the laminator top cover closes, the bending of the PTFE sheet leaves the diaphragm vulnerable to EVA attack.
5. Stretching the diaphragm excessively and making it overly tight can lead to early tearing.
6. Avoiding understretching the diaphragm is important. If the membrane sags, it can expose it to outgassing leakage.
7. Excessively tight clamping can lead to the diaphragm being cut at the corners.
Guidance On Improving Longevity Of silicone Diaphragms
Deer Hunter prioritizes the durability of their PV diaphragms by using high strength materials and following industry standards for thorough preparation. This ensures that the diaphragms are able to withstand various factors that may affect their longevity.
In summary, the following guidelines could assist in maximizing the longevity of your valuable diaphragms.
(1) Safeguarding the working surface with a PTFE/Fabric sheet placed between the membrane and the module
(2) Periodically clearing away the EVA deposits
(3) Preventing sharp edges from piercing the membrane
(4) Installing strictly as per the manufacturer’s guidelines – avoid shortcuts, as installation demands precision
(5) Applying tension carefully – avoid excessive stretching
(6) Regularly re-tensioning the Membrane can mitigate stress on the typical weak points at corners/sides
(7) Ensuring proper vacuum levels in both upper and lower chambers
High Functional Diaphragm Recommended For Laminating Photovoltaic Module
We understand our customers’ demands: unwavering performance, accuracy, efficiency, and cost-effectiveness. These factors drove the development of the Solar 5 Generation (abbr: S5).
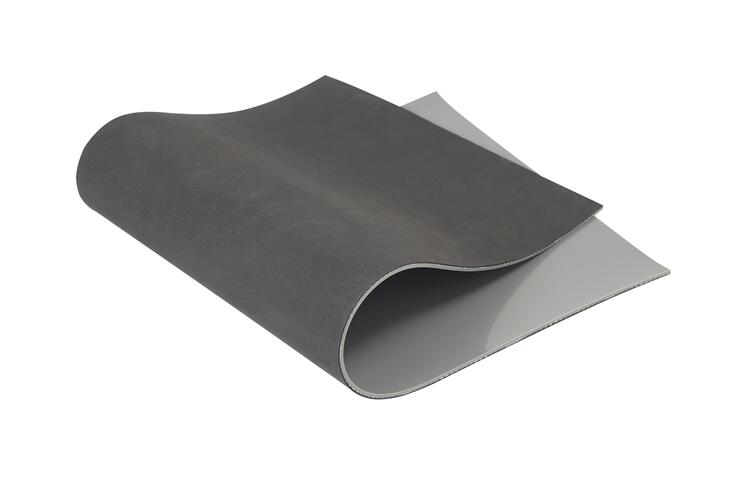
The S5 Solar Diaphragm – The Solution to the Problems
The Solar 5 Gen P.V. diaphragms are specially created to serve as vacuum membranes for the lamination of solar photovoltaic modules. These membranes are engineered with polymers to provide users with exceptional thermal and mechanical properties, as well as good chemical resistance, ensuring a long-lasting and efficient performance.
It offers a multitude of additional benefits, which include:
(1) Seamless one-piece membrane with max width up to 3800mm
(2) A well-received and cost-effective option
(3) Demonstrated reusability under high temperatures
(4) Outstanding release characteristics
(5) Exceptional drawdown strength and resilience
(6) Featuring fabric reinforcement in the middle and an exclusive black hybrid composite as the working side
(7) All membranes undergo thorough post-curing for maximum mechanical attributes
(8) Readily available in stock
Inspection And Storage After Receiving Diaphragms
Well, once the diaphragm sheets leave our factory and arrive at your workshop. What should you do next?
Firstly, perform immediate goods inspection upon product arrival at your workshop.
Secondly, verify the diaphragm condition, sizes, and quantity received.
Thirdly, keep PV diaphragms in their original packaging; avoid placing heavy items on top.
Please find below tips to help you store the rubber sheets.
(1) Store the sheet within a temperature range of -15 to 35 degrees Celsius.
(2) Keep it at least 1 meter away from any heat sources.
(3) Prevent contact with harmful chemicals like oils, acids, alkalis, salts, and others.
(4) Shield it from direct sunlight exposure.
(5) The storage period is valid for twelve months from the production date.
(6) If there is any inconsistency, please communicate with our company’s customer service at the first time.
How To Assemble A Diaphragm In A Laminator?
Fitting a silicone diaphragm onto your solar laminator is a simple procedure, but it’s crucial to diligently follow the manufacturer’s guidelines for correct installation. This ensures proper setup and safeguards the diaphragm and laminator from potential harm.
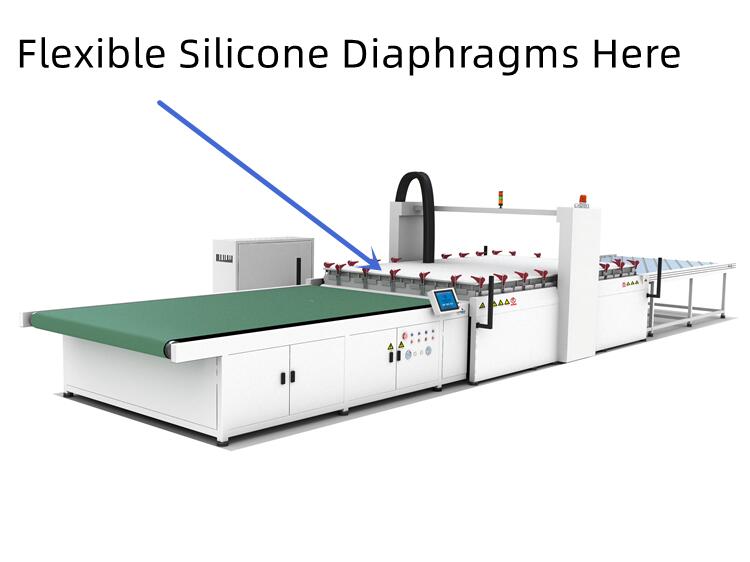
(1) Set the laminator to “Manual” mode.
(2) Ensure no modules are inside the laminator or on conveyor belts.
(3) Remove the old membrane.
(4) Place the S5 Membrane with black EVA (acid resistant) side down onto the module surface.
(5) Spread the new membrane on the heating plate and heat the laminator to 140°C for 30 minutes.
(6) Flatten and heat the membrane for an additional 30 minutes.
(7) Heating for at least 1 hour prevents wrinkles from insufficient stretching.
(8) Stretch the membrane by about 1% after heating for installation.
(9) Use a PTFE / Fabric release sheet between the membrane and module for added protection and longevity. Refer to the service and maintenance notes below.
Service & Maintenance
Silicone membranes are consumable parts subject to wear and tear. For maximum service life, we recommend routine inspections per shift.
Optimal membrane performance is achieved through continuous laminator operation at standard process temperatures (140°/150°C). Intermittent “stop-start” production with temperature fluctuations can reduce rated performance by 500/800 cycles. The vacuum should be checked and restored to the designated process temperature for over 2 hours before resuming production.
Regularly cleaning EVA deposits can be beneficial. If deterioration is noted, timely spare part orders enable membrane replacement at the earliest opportunity.
Regular re-tensioning of the membrane can mitigate stress on typical corner/side weak points.
Prevent EVA buildup and sharp edges on the membrane.
Ensure PTFE belt integrity to prevent EVA leakage into direct contact with the membrane.
As you continue reading, I’d like to address some frequently asked questions that often come up in our daily interactions with customers.
What Is The Best Partner With Solar Silicone Diaphragms?
PTFE(Teflon) coated fabric release sheets are the perfect companions for these silicone rubber diaphragms.
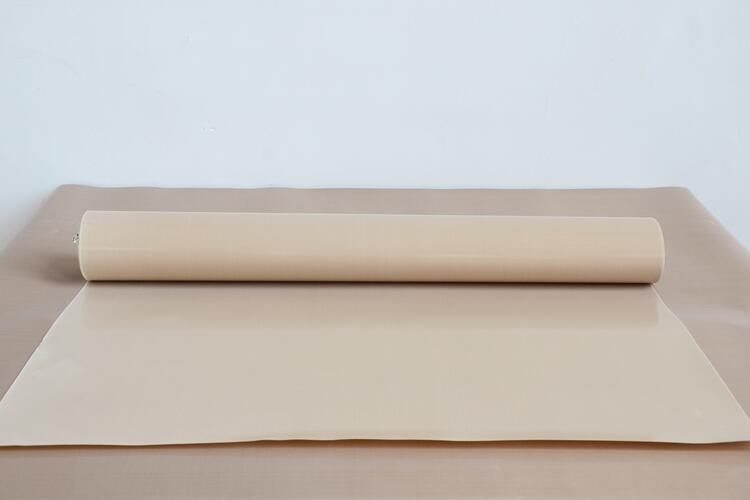
In order to enhance the longevity of the diaphragm, a common practice among our customers involves inserting a layer of polytetrafluoroethylene (PTFE) between the module and the rubber diaphragm. PTFE, a water-resistant and anti-corrosive polymer, offers excellent heat resistance as well. Incorporating a PTFE sheet within the module laminator not only extends the diaphragm’s lifespan but also brings about various production advantages.
In a word, PTFE sheets are the perfect companions for solar silicone membranes. Thickness 0.25mm and 0.35mm are the most frequently ordered from our factory.
Such as:
0.25mm * 2500mm * 25M
0.25mm * 2200mm * 42M
0.25mm * 2280mm * 5910mm
0.35mm * 2350mm * 50M
0.35mm * 2200mm * 2200mm
0.35mm * 2300mm * 6070mm
Top 3 Frequently Asked Questions
Is it a prudent choice to employ membranes with seams?
In our view, seams represent mechanically vulnerable spots. Consistent “draw down” in vacuum conditions can expose any flaws in the seam, ultimately resulting in premature membrane breakdown.
Moreover, seams may occasionally result in undesirable imprint marks on modules – a situation to be avoided!
At Deer Hunter, super-wide membranes in a single piece is easily achievable. We can provide membranes up to 3800mm in width without any seams.
How many cycles do they withstand?
This is the most important and frequently asked question by customers.
To be honest, commonly our data shows that The S5 Gen upto 10,000 cycles. Good life cycle performance under controlled environments, such as humans, temperature, laminating machines, etc. As there are a number of variables beyond our direct control, it is very difficult to “guarantee” an exact cycle life.
Does the color or surface finish affect the performance of the P.V. diaphragm?
Considering any feedback from customers across the globe, we observe no benefits or drawbacks associated with varying colors or surface finishes.
It’s logical to assume that a fabric texture would create a built-in pathway for better release, particularly in hot or adhesive-prone environments. That’s why most of our clients do favor having a fabric texture on one side face down onto the photovoltaic panels.
Conclusion
In the world of solar energy, silicone diaphragms serve as game-changing tools. Their impressive flexibility, strength, and performance improvements offer a path to more effective and long-lasting solar panels. These diaphragms address challenges and lift panel production standards, representing the shift towards cleaner, sustainable energy solutions. As the solar industry aims for excellence, silicone diaphragms emerge as a crucial element in the journey towards a greener future.
Now, I want to hear from you.
For solar panel lamination, are you currently facing any challenging issues?
Could you please share your diaphragm’s size? This will help us provide an offer for your consideration.
OR
If you have differing opinions on some of the points in this blog post, please leave us a comment or directly send us an email to sales@cndeerhunter.com. We can engage in a discussion together and make corrections if needed.
To be continued…