In the vacuum forming industry, two commonly used materials for creating molds are silicone membranes and natural rubber membranes. These vacuum press membranes are versatile and can be used for a variety of applications, such as thermoforming solid surfaces, wood laminations, and composites.
However, it’s important to choose the appropriate type of membrane that can withstand the specific temperature, pressure, and other factors involved in the vacuum forming process to ensure optimal results.
In this blog post, we will compare silicone and natural rubber membranes, examining their similarities and differences, pros and cons, and where and how to order each. Our goal is to help you determine which one is the better option you think for your vacuum presses.
Definitions
Elastomers are materials with elastic properties, meaning they can be stretched and then return to their original shape. Both silicone and natural rubber membranes fall under this category, making them popular choices for various applications. Whether it’s for sealing, cushioning, or insulation, these elastomers provide flexibility and durability that make them essential in many industries.
What are silicone membranes?
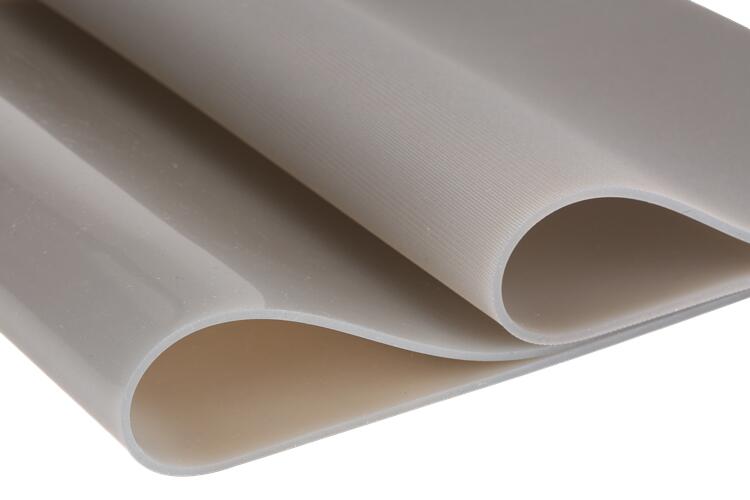
Silicone membranes are versatile sheets or rolls made of silicone rubber that are utilized in a variety of industries. They are particularly useful in vacuum forming and heat press applications due to their high temperature resistance, elasticity, and durability.
These membranes are commonly used in woodworking, thermoforming, sublimation, automotive, and composites. They come in various sizes, thicknesses, and surface finishes to meet the specific needs of each application.
What are natural rubber membranes?
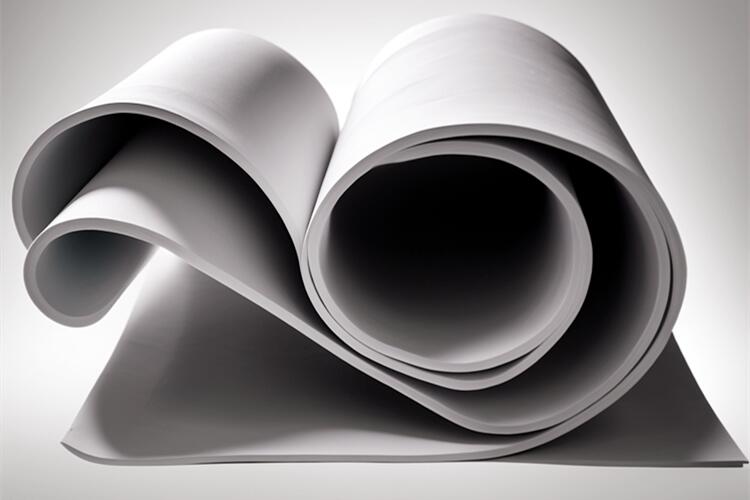
Natural rubber membranes are utilized as top-notch rubber sheets for veneering and laminating purposes in the wood and furniture industry. These membranes possess exceptional properties such as high tear strength, high elongation, and remarkable heat ageing capabilities.
They are compatible with vacuum and membrane presses and can withstand working temperatures of up to 130°C, making them an excellent choice for laminating various materials like veneer, paper, leather, and PVC foil. Additionally, they are also used for shaping furniture components.
Basic Technical Specifications
If you are torn between choosing natural rubber or silicone membranes, it’s important to consider their unique technical specifications and how they align with the specific application at hand. While both materials have their own strengths and weaknesses, selecting the right one can make all the difference in achieving optimal performance and durability.
Natural rubber membranes are a popular choice for woodworking vacuum presses and wood lamination machines due to their exceptional properties.
These membrane sheets are highly elastic, resistant to high temperatures, and incredibly durable, making them ideal for use in both cold and warm vacuum press processes. Their reliability and effectiveness have been proven time and time again in the woodworking industry.
Hardness | Shore A 42 |
Elongation | 700% |
Tear strength | 60N/mm |
Tensile strength | 20Mpa |
Working temperature | Max 130ºC |
Color | Grey |
Surface | Smooth on both sides |
Thickness | 2mm, 2.5mm, 3mm, 4mm |
Width | 1600mm, 2000mm |
Length | 16M |
Silicone membranes are a versatile tool in the manufacturing industry, particularly in the process of vacuum forming solid surfaces and thermoplastics, such as Corian, Hi Macs, Staron, Hanex, Kerrock and others.
These membranes are highly valued for their ability to withstand high temperatures and maintain elasticity, making them ideal for use in hot press and thermoforming applications. Whether creating composite materials or shaping intricate designs, silicone membranes are a reliable and effective solution.
Hardness | Shore A 40-45 |
Elongation | 860% |
Tear strength | 45N/mm |
Tensile strength | 11.5Mpa |
Working temperature | Max 250ºC |
Color | Grey transparent |
Surface | Smooth/Smooth and Smooth/Textured |
Thickness | 1mm, 2mm, 3mm |
Width | Max up to 3800mm |
Length | Any |
Similarities and Differences
While silicone membranes and natural rubber membranes may seem similar at first glance, there are notable differences between the two. Understanding these differences is important when choosing the right material for a specific application.
Heat Resistance and Durability
Silicone membranes are highly valued for their ability to withstand high temperatures, making them a popular choice for industrial vacuum presses that involve extreme heat. With a resistance of up to 250°C, these membranes are particularly useful in thermoforming and hot pressing processes, where high temperatures are required to shape and mold materials.
While natural rubber membranes are less heat-resistant and can only handle temperatures up to 130°C, silicone membranes are a better choice for materials that require higher temperatures, such as solid surfaces. So, if you’re working with high-temperature materials, it’s best to opt for silicone membranes.
In terms of strength and durability, natural rubber membranes are a top choice. They are particularly well-suited for veneering and laminating wood and furniture due to their high tear strength.
However, if you need to create intricate shapes and details, silicone membranes are the way to go. They are incredibly elastic and can stretch up to 860%, making them perfect for molding and shaping.
Elongation and Tear Strength
As mentioned earlier, natural rubber membranes have higher tear strength, which makes them a top choice for woodworking and furniture manufacturing. However, they do have their limitations, particularly when it comes to elongation capabilities. For more complex and detailed projects, silicone membranes may be a better option, as they can stretch up to 750-860% and are better suited for forming intricate shapes and details.
Surface Finish and Textured
When deciding between silicone and natural rubber membranes, it’s important to take into account the surface finish and texture. Silicone membranes have a smooth surface that allows for consistent air evacuation, resulting in high-quality sublimation.
However, natural rubber membranes may have a slightly textured surface that can impact the final outcome of the vacuum pressing process. It’s important to consider which surface finish will best suit your needs before making a decision.
Pros and Cons of Silicone and Natural Rubber Membranes
When considering which type of membrane to use, it’s important to evaluate the advantages and disadvantages of both silicone and natural rubber. This involves examining their technical specifications and unique features to determine which material is best suited for the intended application.

Pros of Silicone Membranes
- Excellent high-temperature resistance, up to 250 ºC, making them ideal for hot press and thermoforming applications.
- Exceptional elasticity, providing a more significant range of elongation without losing its original form.
- Smooth surface finish, making it easy to clean and maintain.
- Highly durable and long-lasting, with excellent tear strength that can withstand heavy-duty use.
- Resistant to chemical and environmental degradation, making them suitable for use in harsh environments.
Cons of Silicone Membranes:
- More expensive than natural rubber membranes.
- Less flexible than natural rubber membranes, which may impact the quality of the final product when working with materials that require more flexibility.
Pros of Natural Rubber Membranes:
- High elasticity, making them ideal for forming intricate shapes and patterns.
- High-temperature resistance, up to 130 ºC, suitable for use in both cold and warm vacuum press processes.
- Superior tear strength, making them suitable for heavy-duty use and repetitive applications.
- Lower cost compared to silicone membranes.
- Excellent elongation properties, making them suitable for vacuum pressing larger and more complex molds.
Cons of Natural Rubber Membranes:
- Can be affected by chemical and environmental degradation, requiring more frequent replacements.
- Not suitable for high-temperature applications above 130 ºC.
- Surface finish can be rough, making it more challenging to clean and maintain.
Factors To Consider When Choosing A Membrane
When choosing a membrane for your vacuum press, there are several factors to consider. These include the type of materials you will be working with, the temperature requirements of your application, the level of grip needed, and the durability and maintenance requirements of the membrane. By carefully considering these factors, you can choose the membrane that will provide the best results for your specific needs.
Material:
The vacuum press membrane should be made of a material that is durable, flexible, and heat-resistant. Common materials include silicone, polyurethane, and PVC.
Thickness:
The thickness of the membrane will affect its durability and flexibility. Thicker membranes are generally more durable but may be less flexible.
Texture:
The texture of the membrane can affect the quality of the vacuum seal. Smooth membranes are typically better for flat surfaces, while textured membranes are better for curved or irregular surfaces.
Size:
The size of the membrane should match the size of the vacuum press. It should be large enough to cover the entire surface area of the workpiece.
Compatibility:
The membrane should be compatible with the type of glue or adhesive being used in the vacuum press.
Cost:
The cost of the membrane is an important factor to consider, as it can vary widely depending on the material and size.
Manufacturer:
Consider the reputation of the manufacturer and the quality of their products when choosing a vacuum press membrane.
Application:
The type of project and the materials being used will also impact the choice of membrane. For example, some membranes are better suited for woodworking, while others may be better for laminating or thermoforming.
Where to Order Silicone and Natural Rubber Membranes?
Before purchasing natural rubber membranes or silicone membranes, it’s important to find a supplier that you can trust. With so many different manufacturers and options available, it can be challenging to determine which supplier will provide the most consistent and high-quality materials. To ensure that you get the best possible product, it’s essential to do your research and choose a reputable supplier that you can rely on.
Natural rubber membranes are widely used in the woodworking and furniture industry, and there are several companies that specialize in their manufacturing and distribution. Some of the most well-known suppliers include Global, Vacuum Pressing Systems, and Veneer Systems, among others. These companies offer a variety of natural rubber membranes in different sizes, thicknesses, and specifications to cater to the diverse needs of various applications.
Silicone membranes are widely used in the vacuum forming and composite industries, and there are many reputable suppliers and manufacturers that offer high-quality products. Some of the most well-known companies in this field include Deer Hunter, Stockwell Elastomerics, and Bellofram Silicones, among others. These companies provide a variety of silicone membranes with different properties and specifications, such as temperature resistance, hardness, and elongation, to meet the diverse needs of various applications.
How To Order?
In terms of purchasing natural rubber or silicone membranes, the internet provides a convenient way to order from a variety of suppliers and manufacturers. However, it’s crucial to choose a reputable supplier that offers reliable shipping and excellent customer service to ensure a seamless ordering experience. It’s also wise to compare prices and specifications from different suppliers to ensure that you’re getting the best possible value for your investment.
To order natural rubber or silicone membranes, the following steps should be taken:
- Determine the required membrane type and size based on the intended application.
- Conduct research to find reputable suppliers through reliable sources such as Google or other online marketplaces.
- Request quotations from several potential suppliers, based on the desired quantity and specifications.
- Review the quotations and negotiate prices if necessary.
- After selecting a supplier, provide shipping details such as the shipping address, preferred carrier, and delivery timeline when placing the order.
- Make payment according to the agreed-upon terms.
- Track the shipment to ensure timely delivery.
- Upon delivery, inspect the shipment for damages or defects.
- Store the membranes properly to avoid degradation until they are needed for use.
- Follow up with the supplier to provide feedback and maintain a good business relationship.
Conclusion
In summary, both natural rubber and silicone membranes have their advantages and disadvantages when it comes to vacuum pressing.
Natural rubber membrane is more affordable and has better elasticity, but it may not be suitable for applications that require high temperature or chemical resistance.
Silicone membrane, on the other hand, is more expensive but offers better durability and resistance to heat and chemicals. Ultimately, the choice between the two materials will depend on your specific needs and budget. We recommend carefully considering all factors and consulting with a vacuum press expert before making a final decision.
Now, it’s your turn. I want to hear from you.
Have you made a decision to select natural rubber or silicone membranes?
Or
Maybe you still have a question about how to pick up the right membrane.
Either way, let me know by leaving an inquiry from the right table sheet.