If 3D laminates were a Hollywood blockbuster, the silicone sheet would be the unsung hero, the stunt double who takes all the hits but never gets the credit. While everyone admires the flawless, seamless finish of 3D laminated surfaces, few realize that behind the scenes, a humble yet mighty silicone membrane is doing all the hard work.
Think of it as the trusty sidekick in a superhero movie. It’s flexible, heat resistant, and always there to ensure everything sticks—literally. Without it, air bubbles would crash the party, adhesives wouldn’t bond properly, and that sleek, high-end finish would turn into a laminating disaster.
But not all silicone sheets are created equal. Choosing the right one is like picking the perfect pizza crust—it needs the right thickness, the right texture, and just enough stretch to hold everything together without tearing apart. Factors like hardness, surface finish, and tensile strength all determine which silicone sheet is the best fit for your vacuum press.
In this blog, we’ll uncover the secrets of silicone sheets for 3D laminate—why they’re essential, how to choose the best one, and the expert tips that will help you achieve perfect laminates every time. So buckle up, we’re about to dive into the world of high tear resistant silicone sheets and why they deserve the spotlight in your lamination process.
Now, let’s get started.
What is a 3D Laminate or Thermofoil?
3D laminate, also known as thermofoil or RTF (Rigid Thermofoil), is a decorative film that can be molded into three-dimensional shapes. Unlike traditional laminate sheets or boards, 3DL comes in a continuous roll and is designed to wrap around a substrate using heat and pressure. It conforms seamlessly to contoured surfaces, eliminating the need for edge banding and providing a smooth, uninterrupted finish.
When used for kitchen doors, drawers, and furniture, 3D laminates cover all five exposed faces, ensuring a uniform appearance without visible seams. This makes them easy to clean, highly durable, and visually appealing.
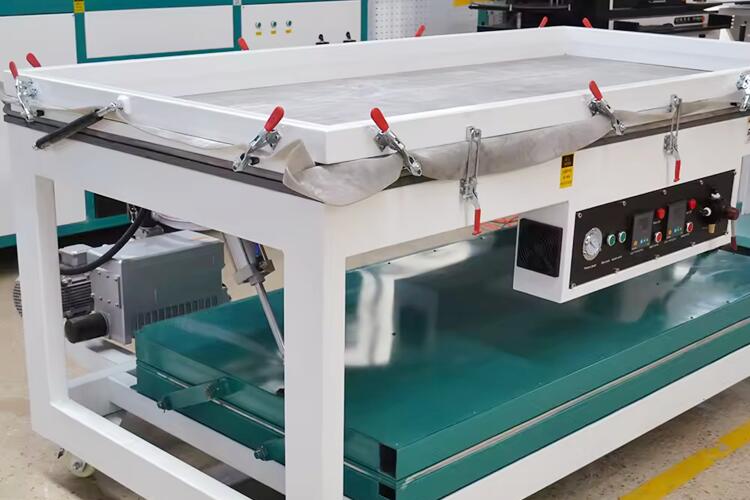
Why Choose 3D Laminates?
3D laminate is a game-changer for achieving high-quality, seamless surfaces. It offers:
- Design Flexibility – Adapts to curved and complex shapes with ease.
- Cost-Effectiveness – More affordable than alternative surfacing materials.
- Water Resistance – Provides a protective, non-porous barrier.
- Mold Prevention – Resistant to moisture-related damage.
- Easy Maintenance – Smooth, seamless surfaces simplify cleaning.
- Long-Lasting Durability – Withstands daily wear and tear.
- Versatile Applications – Used in furniture, cabinetry, healthcare, hospitality, and more.
3D vs. 2D Laminates
When it comes to decorative surfaces, 3D (3DL) and 2D (2DL) laminates provide stylish, durable, and functional solutions across commercial and residential applications. While both are made from thermoplastic films and serve similar purposes, their capabilities set them apart.
What Makes 3D Laminates Unique?
- Seamless Coverage: Unlike 2DL, 3DL wraps around contoured surfaces and edges, eliminating the need for edge banding.
- High Durability: Resistant to impact, chipping, and cracking, making it ideal for high-traffic areas.
- Hygienic & Moisture-Resistant: Seals the substrate, preventing bacteria buildup—perfect for healthcare, office furniture, and retail spaces.
- Unmatched Design Flexibility: Can be formed into shapes, logos, routed MDF panels, and curved components, expanding creative possibilities.
Where Are 3D Laminates Used?
✔ Retail Displays & Fixtures – Offers a sleek, seamless finish with long-lasting durability.
✔ Countertops & Cabinetry – Ideal for kitchens, commercial spaces, and hospitality furniture.
✔ Healthcare & Medical Applications – Resistant to moisture and bacteria, commonly used for hospital tray tables and furniture.
✔ Custom MDF Designs – Forms around intricate shapes, perfect for logos, decorative panels, and unique design elements.
What About 2D Laminates?
- Flat Surface Application: 2DL is mainly used for flat lamination and profile wrapping but requires matching edge banding for a complete look.
- Cost-Effective for Large Surfaces: A great choice for walls, ceilings, and commercial panels where seamless edges aren’t a priority.
- Material Flexibility: Available in both film-based and paper-based formats, catering to different durability needs.
Where Are 2D Laminates Used?
✔ RV Interiors & Commercial Walls – Lightweight, durable, and cost-efficient for large surface applications.
✔ Retail Fixtures & Store Displays – Used for flat signage, shelving, and decorative trims.
✔ Moldings & Profile Wrapping – Applied to edge trims and architectural components for a polished finish.
Both 3DL and 2DL offer excellent design and performance benefits, but selecting the right one depends on your specific needs. For seamless, contoured designs, 3DL is the way to go, while 2DL is best for cost-effective, flat-surfaced applications.
If you need high-performance rubber sheets for your 3D laminate projects, Deer Hunter has you covered. Contact us today to find the perfect silicone membrane for your needs!
Silicone Sheets: A Key Component in 3D Laminates
Silicone sheets are a critical component in 3D lamination, enabling vacuum presses to deliver precise, high-quality results. Their primary functions are twofold:
- Efficient heat transfer – They help distribute heat evenly across the laminated surface, ensuring the adhesive activates properly.
- Consistent pressure application – They exert uniform pressure over the workpiece while the vacuum underneath creates suction, eliminating air pockets and imperfections.
This combination results in faster cycle times and the ability to achieve intricate design details that would be difficult with traditional lamination methods.
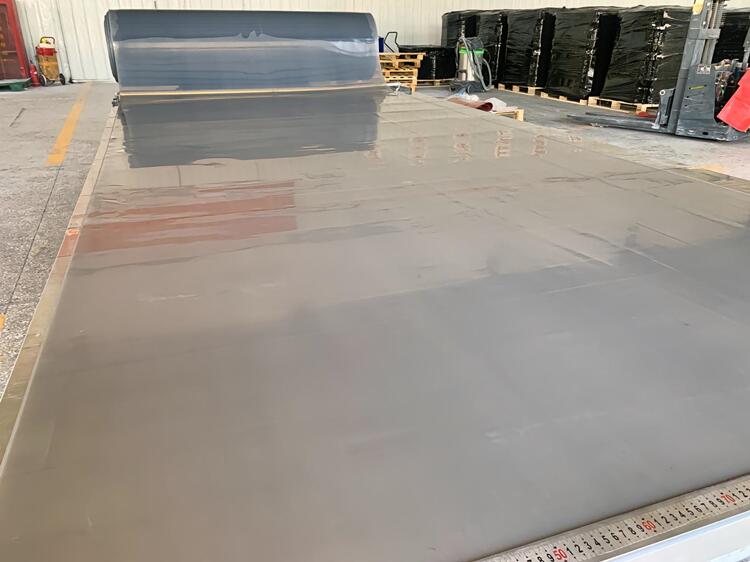
Do Silicone Membranes Need Replacement?
Like any essential tool, silicone membranes don’t last forever. Their lifespan depends on the number of cycles and the complexity of the parts being produced. Over time, wear and tear may necessitate replacement.
Additionally, investing in a membrane press can be a significant upfront cost—ranging from $20,000 to over $50,000—though used or budget-friendly options are available. Keep in mind that not all vacuum presses can function without a membrane, making it a necessary investment for precision lamination.
Vacuum Press Brands Compatible with Silicone Membranes
Many vacuum presses worldwide rely on silicone membranes for their lamination processes. Some of the most recognized brands include: Global, Columbus, Barth, Orma, BYT, Felder, etc.
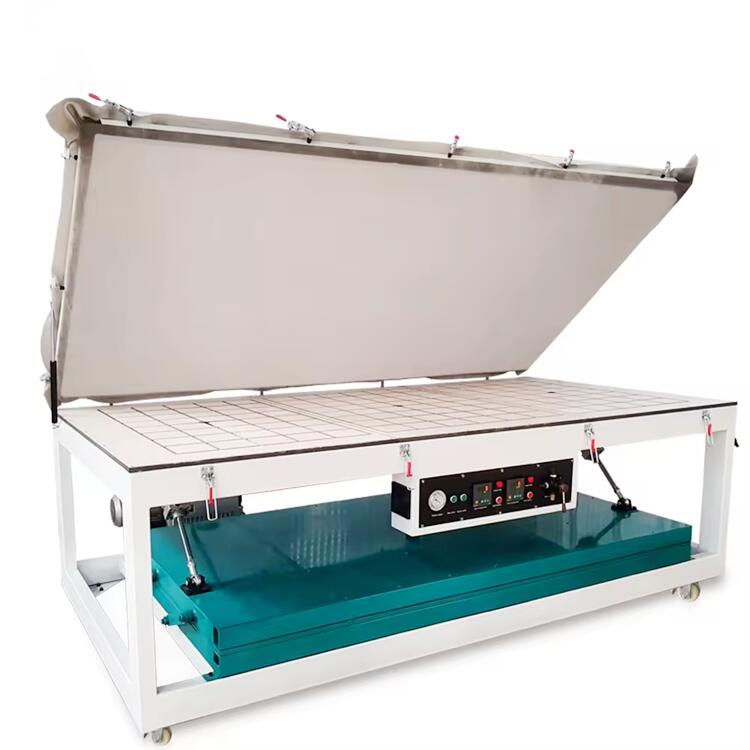
If you’re a vacuum press manufacturer and don’t see your company listed, feel free to contact us—we’re happy to update this section.
Silicone sheets are the go-to choice for vacuum membrane presses due to their unique properties:
- High heat resistance – They withstand extreme temperatures without deforming, ensuring consistent pressure throughout the process.
- Superior flexibility – Their elasticity allows for uniform bonding, even on complex or contoured surfaces.
- Non-stick surface – Prevents adhesive buildup, reducing the need for frequent cleaning and minimizing downtime.
- Cost-effective & reusable – With proper care, silicone vacuum sheets can be used multiple times, making them a long-term, value-driven solution for 3D lamination.
For manufacturers aiming for seamless, durable, and high-quality laminated finishes, silicone membranes are an indispensable asset in the production process.
Understanding Silicone Sheets in 3D Lamination
Silicone membrane sheets play a crucial role in 3D lamination by acting as a protective barrier between the lamination material and the vacuum press. Their job is to ensure a flawless finish by preventing air pockets, controlling adhesive spread, and evenly distributing heat and pressure. The result? A perfectly laminated surface that is both durable and visually appealing.
Step-by-Step Process of 3D Lamination with Silicone Membranes
- Barrier Against Air Pockets & Imperfections
Silicone membranes create an airtight seal over the material, eliminating trapped air that could cause bubbles or defects. This ensures a smooth, seamless finish with no distortions.
- Even Heat & Pressure Distribution
As the vacuum press activates, the silicone membrane conforms tightly to the material, ensuring consistent heat and pressure across the entire surface. This allows adhesives to bond evenly, creating a strong, long-lasting hold.
- Protection Against Heat Damage
Silicone membranes shield the material from direct exposure to heating elements, reducing the risk of discoloration, burns, or warping—especially for delicate or heat-sensitive materials.
How the Process Works
- The silicone membrane is placed over the workpiece inside the vacuum press.
- A vacuum is applied, pulling the membrane tightly against the substrate, eliminating air pockets.
- Heat and pressure activate the adhesive, securing a strong, even bond.
- The result is a seamless, high-quality laminate that maintains its structure and aesthetic appeal.
Silicone membranes don’t just enhance the bonding process—they also extend the lifespan of laminated products by preventing imperfections and ensuring optimal adhesion.
The Value of Silicone Sheets in 3D Laminates
Silicone sheets bring significant benefits to the 3D lamination process, ensuring seamless finishes, efficient production, and long-term durability. Whether you’re laminating furniture, automotive interiors, or architectural elements, these membranes help elevate quality and streamline operations.
Why Use Silicone Membrane Sheets?
✔ Flawless, Seamless Finish
Silicone membranes eliminate imperfections, ensuring bubble-free, smooth surfaces that enhance the final product’s aesthetics.
✔ Even Pressure Distribution
By applying uniform pressure, these membranes prevent uneven bonding, guaranteeing a strong and reliable adhesive connection between the lamination material and the substrate.
✔ High Heat Resistance
Designed to withstand extreme temperatures, silicone vacuum sheets maintain their shape without deforming, allowing the lamination process to run at optimal heat settings for a secure, lasting bond.
✔ Low Maintenance & Easy Cleaning
Silicone’s non-stick properties prevent adhesive buildup, minimizing downtime and ensuring continuous, efficient production with less frequent cleaning.
✔ Cost-Effective & Reusable
With proper care, silicone vacuum sheets last through multiple production cycles, making them a long-term, cost-saving investment. Their durability reduces material waste and replacement costs.
For manufacturers and designers looking to achieve flawless, high-quality 3D laminated products, silicone membranes are an essential tool that enhances both efficiency and final product excellence.
What to Consider When Selecting a Silicone Membrane
Selecting the right silicone sheet is key to achieving consistent, high-quality 3D laminates. The right choice depends on factors such as thickness, hardness (durometer), and tear resistance—all of which affect flexibility, durability, and performance. Let’s break down what you need to consider when choosing the perfect silicone membrane for your project.
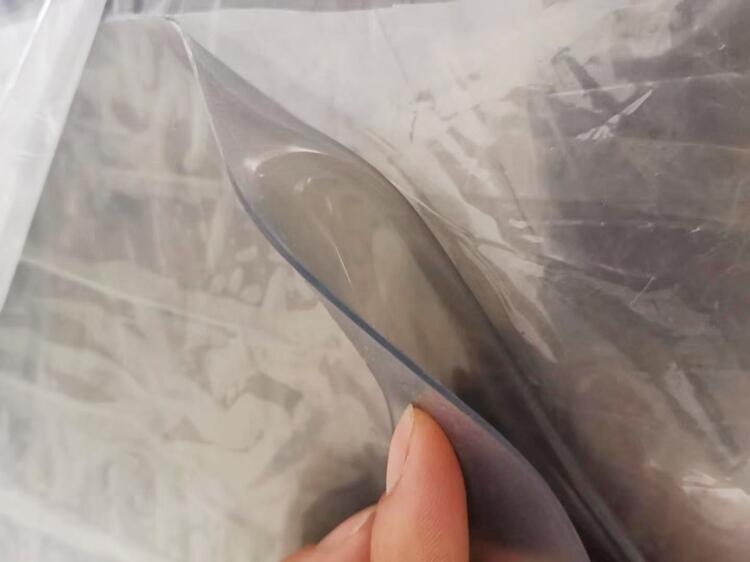
1: Thickness – Balancing Flexibility & Heat Resistance
Silicone membranes come in different thicknesses, ranging from thin sheets for intricate details to heavy-duty options for demanding applications.
✔ Thinner membranes (1mm and 2mm): More flexible, ideal for complex curves and delicate designs.
✔ Thicker membranes (3mm and above): Higher heat resistance and durability, best for larger or high-pressure applications.
2: Durometer – Finding the Right Hardness
Durometer measures the hardness of the rubber, affecting how a membrane stretches and responds under pressure. It is assigned a value from 5 to 100, with a tolerance of ±5.
There are three main durometer types:
✔ Type A – For soft rubber, commonly used in standard vacuum forming applications.
✔ Type D – For hard rubber, suited for high-pressure and industrial laminations.
✔ Type 00 – For sponge and foam, ideal for applications requiring extreme flexibility.
For 3D lamination, most manufacturers prefer Type A membranes in the 40–50 durometer range, offering a good balance of flexibility and strength.
3: Tear Resistance – Ensuring Longevity
Tear resistance is crucial for membranes subjected to frequent use or high-pressure cycles. A membrane with high tear resistance lasts longer, reduces downtime, and enhances overall efficiency.
✔ Higher tear resistance = Longer lifespan & better performance
✔ Ideal for high-production environments & heavy-duty applications
4: Specialized Membranes for Unique Applications
Beyond standard silicone membranes, there are specialized options designed for specific needs:
- Anti-static membranes – Prevent static buildup, reducing the risk of damage to sensitive electronic components.
- Non-marking membranes – Leave no residue or marks on laminated surfaces, ideal for high-precision finishing.
Choosing the right silicone membrane isn’t just about picking a sheet—it’s about optimizing performance for your specific 3D lamination process. By carefully considering thickness, hardness, tear resistance, and special features, manufacturers can ensure peak efficiency, durability, and flawless results.
Effective Ways to Maximize Silicone Sheet Performance
Selecting the right silicone membrane is just the first step—using it effectively ensures flawless results and extends its lifespan. Below are key best practices to maximize performance and avoid costly mistakes in 3D lamination.
1: Match the Membrane to Your Application
Each lamination project has unique requirements, so choosing the right membrane depends on:
✔ Size & shape of the substrate – Complex or curved designs require thinner, more flexible membranes.
✔ Laminated material type – Different materials may need specific membrane properties (e.g., heat resistance, anti-static).
✔ Production demands – High-volume production requires durable, tear-resistant membranes for long-term efficiency.
2: Ensure Material Compatibility
Not all silicone membranes work with every material. Some require high heat resistance, while others need anti-static properties to prevent static buildup in sensitive applications. Always check compatibility with adhesives and substrates to achieve the best results.
3: Invest in Quality & Durability
✔ Cheap membranes cost more in the long run. Lower-quality options may wear out quickly, leading to inconsistent results and frequent replacements.
✔ Choose reputable manufacturers that provide tested, high-performance silicone membranes for reliability and longevity.
4: Consider Long-Term Cost-Effectiveness
✔ Higher-quality membranes may have a higher initial cost but offer better durability, performance, and fewer replacements, leading to lower total costs over time.
✔ Evaluate the return on investment (ROI)—a well-selected membrane can increase production efficiency and reduce waste.
5: Leverage Expert Recommendations
If you’re unsure which silicone membrane fits your needs, seek advice from industry professionals. Experienced laminators and suppliers can help optimize your selection based on real-world applications.
By carefully considering application requirements, material compatibility, durability, cost-effectiveness, and expert advice, you can maximize efficiency and product quality while reducing downtime. A well-chosen and well-used silicone membrane is the key to flawless, high-performance 3D lamination.
Pitfalls When Using Silicone Membranes
Silicone membranes are essential for achieving flawless 3D laminates, but avoidable mistakes can compromise their effectiveness. Below are the most common errors—and how to prevent them—to ensure optimal performance and longevity.
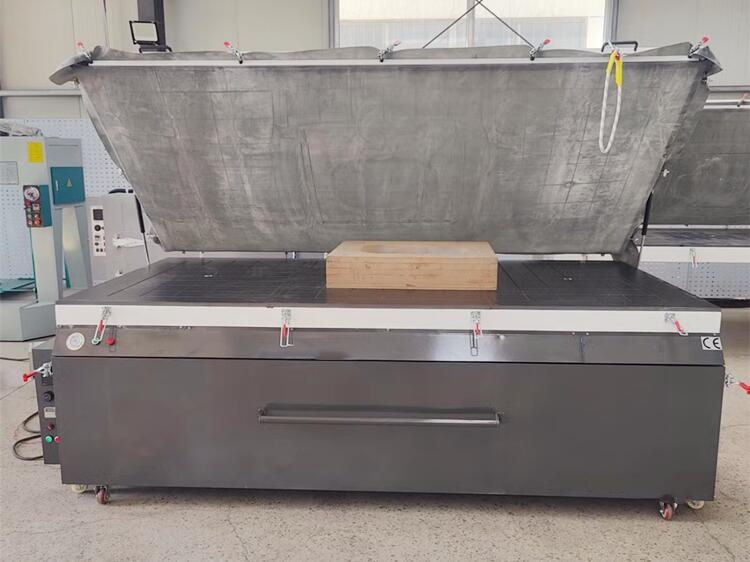
1: Choosing the Wrong Silicone Membrane
✔ Using a membrane with the wrong thickness, durometer, or tear resistance can lead to poor adhesion and inconsistent results.
✔ Always match the membrane specifications to your project’s heat, pressure, and durability requirements.
2: Incorrect Positioning
✔ Wrinkles or misalignment can cause uneven pressure distribution, leading to air bubbles, weak bonds, or surface imperfections.
✔ Ensure the membrane is smooth, properly stretched, and evenly covering the workpiece before starting the process.
3: Using the Wrong Vacuum Pressure
✔ Too much pressure can distort materials, while too little can cause weak adhesion.
✔ Test different vacuum settings to find the optimal balance for your specific materials.
4: Inconsistent Temperature Control
✔ Temperature fluctuations can result in adhesive failure or uneven bonding.
✔ Maintain a consistent, optimal temperature throughout the process to ensure a strong, lasting bond.
5: Neglecting Regular Maintenance
✔ Adhesive buildup can reduce efficiency and damage the membrane.
✔ Clean the membrane regularly according to the manufacturer’s guidelines and store it properly when not in use.
Avoiding these common mistakes ensures that your silicone membranes deliver consistent, high-quality results while maximizing their lifespan. A well-chosen, properly maintained membrane can significantly improve efficiency and product quality in 3D lamination.
Practical Uses of Silicone Sheets in 3D Lamination
Silicone sheets are transforming multiple industries by delivering seamless finishes, enhanced durability, and precision bonding in 3D lamination. Below are real-world applications showcasing how manufacturers and designers leverage silicone membranes for superior results.
1: Furniture Industry: Achieving Flawless Decorative Laminates
Silicone membranes are widely used in furniture manufacturing to laminate tabletops, cabinet doors, and paneling. Their ability to apply uniform pressure ensures:
✔ Seamless, bubble-free finishes that enhance the visual appeal.
✔ Improved durability, making laminated furniture more resistant to daily wear.
✔ Versatility, accommodating both flat and contoured surfaces.
2: Automotive Industry: Enhancing Interior Components
In the automotive sector, silicone membranes are integral to laminating dashboards, door panels, and trim, where precision and aesthetics are key. Benefits include:
✔ Flawless surface finishes, essential for high-end vehicle interiors.
✔ Heat resistance, ensuring the adhesive bonds remain strong despite extreme temperatures.
✔ Increased longevity, preventing peeling or warping over time.
3: Architectural Applications: High-Quality Decorative Elements
For commercial buildings and residential interiors, silicone membranes provide a perfect lamination solution for decorative panels and wall designs. Their role includes:
✔ Adding depth and texture to architectural elements.
✔ Ensuring strong adhesion for various materials, including wood, MDF, and composites.
✔ Delivering long-lasting performance in both indoor and outdoor applications.
From furniture to automotive interiors and architectural designs, silicone membranes have become an indispensable tool for achieving high-quality, long-lasting laminated surfaces. Their versatility, precision, and durability make them a top choice for manufacturers seeking efficiency and flawless results.
Sealing the Deal
Alright, you’ve made it this far, which means either you really care about silicone membranes or you’re just too polite to stop reading. Either way, we like you already.
By now, you know that not all silicone sheets are created equal—some stretch better, some last longer, and some just make your life easier by refusing to collect adhesive like a toddler with sticky fingers.
So, what’s next? Well, you could take your chances with subpar membranes and watch your laminates cry for help… or you could get it right the first time with Deer Hunter’s high-performance silicone sheets.
Drop us a message, send us a carrier pigeon, or just email us the old-fashioned way at sales@cndeerhunter.com. We promise we’ll respond faster than a vacuum press cycle!
Call/Text/WhatsApp: +86-13823789007
Let’s make your 3D lamination projects smoother, stronger, and stress-free—because life’s too short for bad laminates!